Tasarımcılar ile dökümhane arasında kurulan etkili iletişim sayesinde yüksek kalitede döküm üretimi.
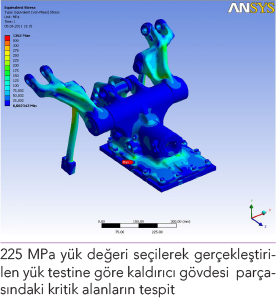
Hema Endüstri A.Ş. dökümhanesinde, karşılaşılabilecek olası problemler gözetilerek; tüm prosesler ilk aşamadan itibaren sıkı bir koordinasyon içinde tasarlanmaktadır. Efektif ve açık bilgi paylaşımı sayesinde gerekli tüm değişiklikler ve proses parametreleri ortaklaşa belirlenip, üretim aşamasına geçmeden önce tüm kriterlerin karşılanması garanti altına alınması sağlanmaktadır. Hema Endüstri bünyesinde faaliyet gösteren Hema Metal işletmesinde parça tasarımlarının dökülebilirlik değerlendirmelerinin başarıyla gerçekleştirilmesi amacıyla MAGMASOFT kullanılmaktadır. Yeni parça devreye alımlarında döküm simülasyon yazılımı kullanımı ile birlikte, üretilen prototip ve yapılan deneme dökümü sayısı parça başına yaklaşık 1,6 deneme oranı ile minimuma indirilmiştir.
“Kaldırıcı Gövdesi” parçası, söz konusu etkili iletişimin meyvelerinden biri olarak göze çarpmaktadır. Gerçek çalışma koşulları göz önüne alınarak maksimum yük değerlerinde gerçekleştirilen CAE analizinde parçanın pik döküm olarak üretilebileceği belirlenmiştir.
Ancak, MAGMASOFT® ile gerçekleştirilen bölgesel analizlere göre parçanın operasyon esnasındaki yük altında yapısını koruyabilmesi için kesit alanlarının daha kalın olması gerektiği tespit edildi. Parça ağırlığının artması ile birlikte üretim maliyeti de artacak ve parçanın montaj ve operasyon koşullarının zorlaşacağı bilgisi müşteri ile paylaşılarak parçanın sfero döküm olarak üretilmesine karar verildi.
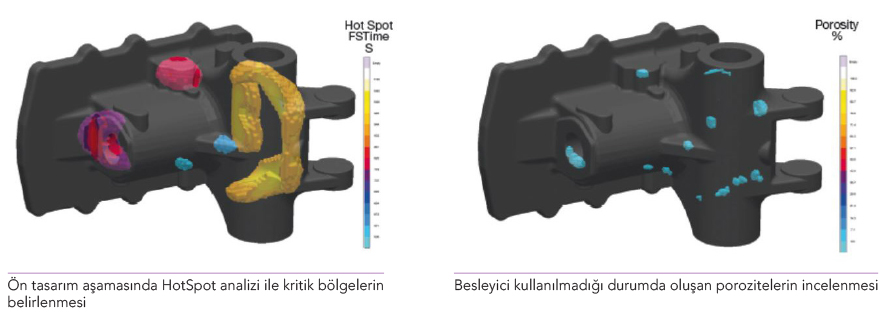
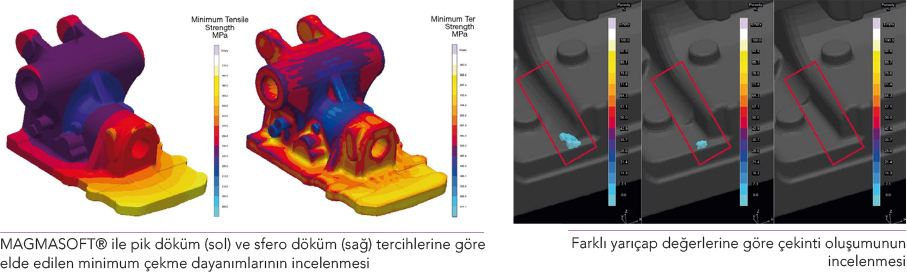
Sfero döküm, pik döküme göre daha fazla besleyiciye ihtiyaç duyuyordu ve bu doğrultuda bir dizi tasarım değişikliği, model revizyonu ve besleyici-yolluk sistemi denemesi yapılmasını gerektirdi.
Kolları sıvayan ve çalışmaya başlayan tasarım ekibi; ilk etapta parçanın ağırlığını düşürmek için bölgesel kesit alanlarını azaltmaya karar verdi. Kesit alanlarının inceltilmesi ile besleyici ihtiyacını düşürerek proses verimini arttırmak hedeflendi.
Kesit alanlarının bölgesel olarak inceltilmesinde MAGMASOFT®’un Otonom Optimizasyon modülünün yeni özellikleri kullanarak muhtemel bir çok seçenek sistematik bir şekilde incelendi. Orijinal tasarımdaki parça yarıçapının büyüklüğü çalışmalar esnasında değişken parametre olarak belirlenerek; hedef kriterleri olarak da porozitenin ve parça ağırlığının minimuma indirilmesi seçildi.
MAGMASOFT® bünyesindeki otomatik değerlendirme araçları ile tüm tasarımlar istatistiksel açıdan kolayca incelendi ve oluşturulan “sıralama” tablosunda, seçilen hedef kriterleri optimum düzeyde karşılayan tasarım ortaya çıkmış oldu. Sıralamada 1 numaralı tasarımın tüm kriterleri yerine getirerek; minimum poroziteyi, arzu edilen mekanik özellikleri ve düşük parça ağırlığını mümkün kıldığı belirlendi.
Elde edilen sonuçlar görsel optimizasyon modülü kullanılarak çubuk grafik üzerinde değerlendirildiğinde; yarıçap değişimlerinin parçanın çekinti eğilimi ve ağırlığı üzerindeki etkileri görüldü. Bu veriler tasarımcılara ve üretimcilere kalite ve maliyet hedeflerini tutturmakta ellerini oldukça güçlendiren kantitatif kanıtlar sundu.
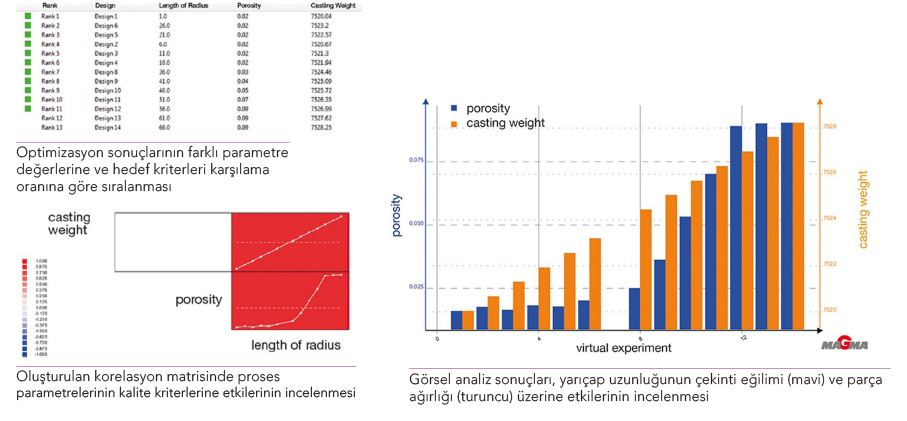
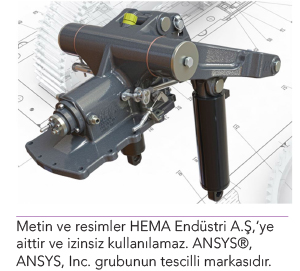
Elde edilen optimum tasarım ve proses parametreleri sayesinde kaldırıcı gövdesinin üretimini başarıyla gerçekleştiren HEMA Metal, sonuçlardan çok etkilendi. Tüm HEMA Metal ekibinde MAGMA Otonom Optimizasyon modülü ile yeni siparişlerin devreye alım çalışmalarına başlama heyecanı ve teknik bilgi birikimlerini daha da ileriye taşıma hedefi gözle görülür şekilde canlılığını koruyor.