Önümüzdeki yıllar içinde metallerin üretiminde katmanlı yöntemler (AM) kullanılmasının (metallerde 3D baskı olarak da bilinir), geleneksel olarak “çıkarmalı” yöntemlerle çalışan üreticilerin üretim konusundaki yaklaşımlarını değiştireceğine hiç şüphe yoktur. Gerçekten de, otomotiv prototipi üretimi ve havacılıktan tıbbi cihazlara ve güç üretimine varan alanlardaki orijinal malzeme üreticileri uzun zamandan beri AM tekniklerini üretim hatlarında kullanmaya başladılar. Dahası, bu yeni teknolojinin avantajlarının üretim sürecinin kendisi kadar, üretimde kullanılacak takım tezgahlarının oluşturulmasında da kullanılabileceği kolayca anlaşılabilir.
Gelişme ve Diğer Yöntemlerle Birlikte Kullanım
Kuşkusuz, katmanlı üretim tümüyle yeni bir yöntem değildir – orijinal olarak 1980’lerin ortasında geliştirilmeye başlanan bu yöntem yedi farklı standart AM teknolojisi altında kategorize edilmiştir ve bunların bazıları metallerde kullanıma uygundur. Uzman şirketler yirmi yılı aşan bir süreden beri lazerli sinterleme işlemiyle metal üzerinde AM kullanmaya başlamış durumdadır. Ancak o günlerden bu yana teknolojideki önemli ilerlemeler sonucunda hem toz yataklı füzyon sistemleri (parçayı oluşturan malzemenin katmanları eritilir) hem de yönlendirilmiş enerji biriktirme (toz üfleme, toz besleme veya metal tozu biriktirme olarak da bilinir) alternatifleri, parçaları ince malzeme katmanlarının birikimi ile oluşturabiliyor.
Bu gelişimi desteklemek üzere katmanlı üretimde kullanılan malzeme türleri de artıyor. Artık atomize metal tozu seçenekleri düşük alaşımlı çeliklerin, takım çeliklerinin, paslanmaz çeliklerin, dubleks çeliklerin, kobalt alaşımlarının, nikel alaşımlarının, alüminyum alaşımlarının ve titanyum alaşımlarının kaplanmasında kullanılıyor.
Gerçekten de, üretim süreçlerinin dereceli bir biçimde gelişmesi öngörülebilir. Bunu sağlayacak olan ise, bir uçtan diğerine değer kattığı gösterilmiş olan AM teknikleri desteğiyle geleneksel işleme yöntemlerinin verimliliğinin artırılması ve maliyetinin düşürülmesidir. Aslında daha şimdiden katmanlı süreçlerle işleme süreçlerinin kombine edilmesini veya AM sürecinden talaşlı imalata hızlı geçiş olanağı sağlayan karşılıklı değiştirilebilir tezgah başlıklarına sahip hibrit CNC tezgahlarının ortaya çıktığını görebiliyoruz.
Dahası, katmanlı veya çıkarmalı tekniklerin seçimi tahmin edeceğiniz ölçüde “ya biri, ya da diğeri” şeklinde değildir. Pek çok durumda, örneğin bir parçanın katmanlı üretimle hazırlanmasına karar verilse bile, parçanın ince talaş işlemesinde geleneksel talaşlı imalat tekniklerinin kullanılması daha uygun maliyetli veya gerekli olabilir. Örneğin gereken toleransı elde etmek ve yüzey ince işleme taleplerini karşılamak için çok yüksek toleranslara göre baskı yapmak yerine geleneksel talaşlı imalat tekniklerini kullanmak tercih edilebilir. AM tarzı üretim, iş akışının bir parçasıdır ve eğer yüksek toleranslar gerekliyse üretim sonrası uygulama ve işleme gereklidir. Bu tür durumlarda, parçaların gerekenden büyük olarak bastırılması avantaj sağlayabilir; böylece hedef uygulama için gereken son tasarımın sağlanmasında çıkarma (işleme) operasyonu için daha iyi kesme şartları sunulabilir.
Hibrit çözümler içi boş parçaların üretiminde de uygulanabilir. Böyle bir durumda, parçanın üretimi için bir AM prosesiyle başlayıp biten, ancak ortada klasik tezgah kullanımına ihtiyaç gösteren bir senaryo düşünülebilir. Böylece üretim tek bir parça halinde yapılabilir ve montaja gerek kalmaz.
Bir üretici klasik tezgah tekniklerini kullanmayı sürdürse de, eğer kesici takımları uygun biçimde üretilmişse katmanlı üretimden yararlanma şansına sahip olabilir. Her ne kadar uygulamaların büyük çoğunluğunda AM teknikleriyle takımlar oluşturmak ticari bakımdan uygun olmasa da, bu tarz bir üretimin verimlilik iyileşmeleri sağlayacağı bazı alanlar vardır. Baskıyla oluşturulmuş (kafes yapılı) bir takımın sağlayacağı avantajlara örnek olarak ağırlığının daha hafif olması sayılabilir. Böylece uzun kullanma mesafesine sahip parçaların işlenmesi sırasında verimliliğe ve kaliteye zarar verebilecek titreşim yatkınlığı azaltılabilir.
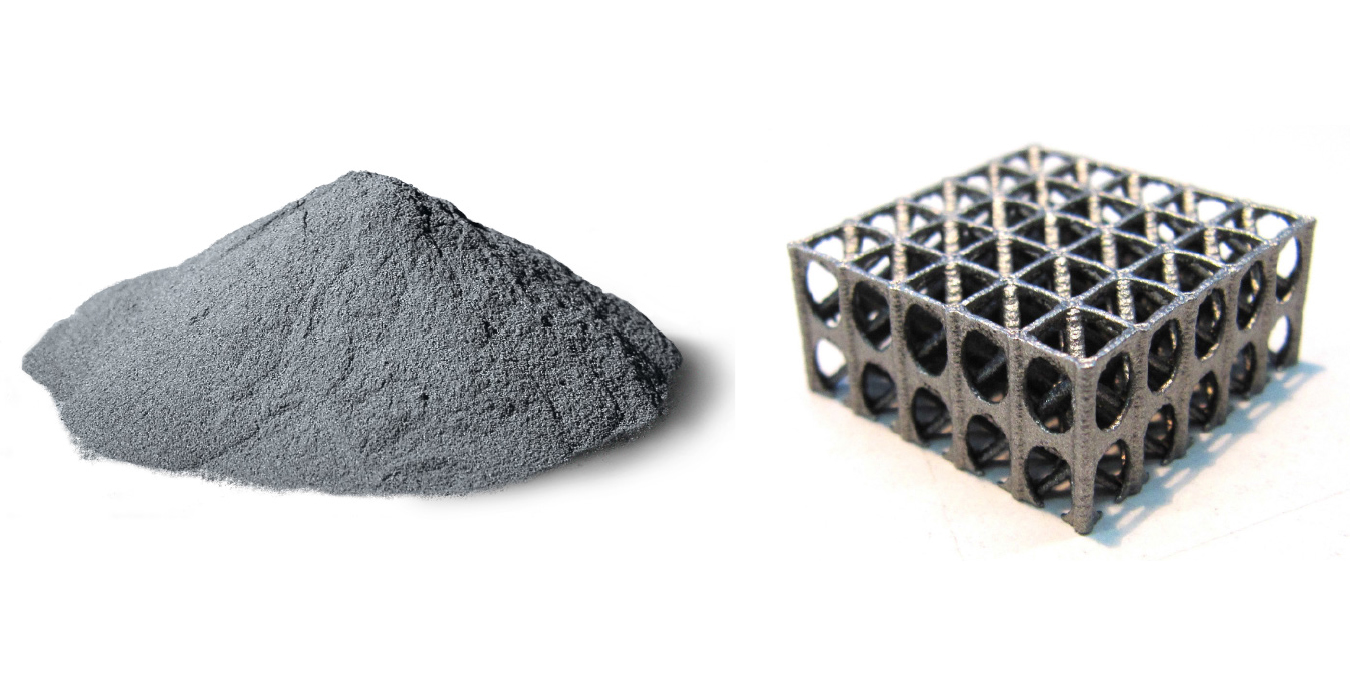
AR-GE
Tezgah üreticileri, takım tedarikçileri, üreticiler ve diğer ilgili taraflar yeni katmanlı imalat prosesleri geliştirmek için Ar-Ge yatırımlarını artırıyor. Sandvik Coromant da bunun dışında kalmıyor; şirket bu yılın başlarında İsveç’te yeni bir AM araştırma tesisinin açılışını yaptı.
Sandvik Materials Technology Sandvik Osprey (toz metalurji dünyasında global bir marka olarak 10 yıllık AM deneyimiyle uygulamada kullanılacak tozlar sunar) gelişmiş toz çözümlerine erişim olanağı bulunan bu tesis Sandvik Coromant’ın 2013 yılından bu yana yürüttüğü çalışmaların bir ürünüdür. Başlıca hedefleri arasında yeni AM çözümlerinin müşteri taleplerini nasıl karşılayabileceğini araştırma, hibrit işleme ve AM tekniklerinin uçtan uca imalat prosesine nasıl değer katabileceğini belirleme ve 3D uygulamalarıyla takım tezgahları oluşturma yeteneğinden yarar sağlayabilecek alanları araştırma sayılabilir.