Aykut DOĞAN(*) Ekrem ALTUNCU
(*)Sakarya Universitesi Müh. Fak. Metalurji ve Mal. Müh. Böl., Esentepe Kampüsü, Sakarya/ Türkiye, 54187
Sakarya Universitesi Müh. Fak. Termal Sprey Tek. Ar&Ge Lab., Esentepe Kampüsü, Sakarya/ Türkiye, 54187
ÖZET:
Bu çalışmada otomotiv sektöründe motor sistemlerinde performans açısından ve motor verimliliği açısından kritik öneme sahip pistonlar için, farklı alüminyum alaşımlarının sıcaklık ile mekanik özelliklerinin değişimi, kimyasal kompozisyonda alaşım elementlerinin ve ısıl işlemlerin mikroyapıya etkileri irdelenmiştir. Son yıllarda artan talepler doğrultusunda yeni nesil alüminyum alaşımları (Al-Si, Al-Fe ve Al-Cu+X:Refrakter metal)üzerine yoğunlaşılmıştır. Özellikle NASA 398 kodlu alüminyum alaşımı (%16 Si)’nın yüksek sıcaklıklarda davranışlarna bağlı olarak mikroyapısal ve mekanik özellikleri incelenerek geleneksel alaşımlar ile karşılaştırılmıştır. Bunun sonucunda ötektiküstü NASA 398 (%16 Si) alaşımının piston için üst çalışma sıcaklıklarında iyi mukavemet ve termal özellikler gösterdiği tespit edilmiştir.
Anahtar kelimeler: Piston alaşımları, Al-Si alaşımları, NASA 398 alaşımı, Yüksek sıcaklık davranışı
1.GİRİŞ
Günümüzde içten yanmalı motorlar yüksek hızlı, yüksek sıkıştırma oranlı, kısa kurslu ve geniş silindir çaplı yapıldıkları için yüksek oranda ısı transfer özelliğine sahip, düşük yoğunluklu ve yüksek sıcaklığa dirençli metaller tercih edilmektedir. Bu nedenle dökme demir ve alaşımlarına alternatif olarak motor pistonlarında günümüzde genel olarak gerek performans gerekse maliyet açısından alüminyum esaslı alaşımlar tercih edilmektedir. Artan çevresel faktörler karşısında otomotiv endüstrisinde önemli kısıtlamalar söz konusu olup, emisyon (Nox) değerlerinin azaltılması ve motor performansının ve verimliliğinin artırılması beklentisinden kaynaklı olarak daha yüksek sıcaklıklarda (T>250oC) çalışabilecek alüminyum alaşımlarına ihtiyaç sürekli artmaktadır. Piston malzemesi olarak kullanılacak yeni nesil alüminyum alaşımlarının düşük yoğunlukları yanında pistonların çalışma sıcaklığına bağlı olarak daha yüksek sıcaklıklara dayanıklı (T>350oC), uzun ömürlü ve yeterli mekanik özellikleri
karşılaması beklenmektedir [1].
Alüminyum alaşımlarının yüksek sıcaklıkta yüksek mukavemet gerektirmesi yeni döküm yöntemlerinin gelişmesini gerektirmiştir. Bu çalışmaların sonucunda güncel olarak metal matris içine sert partikül takviyeli sıkıştırma (squeze) ve savurma (centrifugal) döküm proseslerinin geliştirildiği gözlenmektedir. Özellikle Japonya, Avrupa ve Amerika’da bu yöntemlerle takviyeli, yüksek mukavemetli alüminyum alaşımlarının üretimi gerçekleştirilmektedir. Bu proseslerde küçük taneli mikroyapısal özelliklerin etksiyle yüksek mekanik dayanım elde edilebilmiştir. Hızlı katılaşma prosesinin sonucunda yüksek soğutma hızı nedeniyle alaşım elementlerinin yüksek çözünebilirliğine imkan vermesi yüksek sıcaklığa dirençli alüminyum alaşımı üretimini mümkün kılmıştır [3]. Tablo 1’de alüminyum alaşımlarının genel sınıflandırılması verilmiştir. [3]
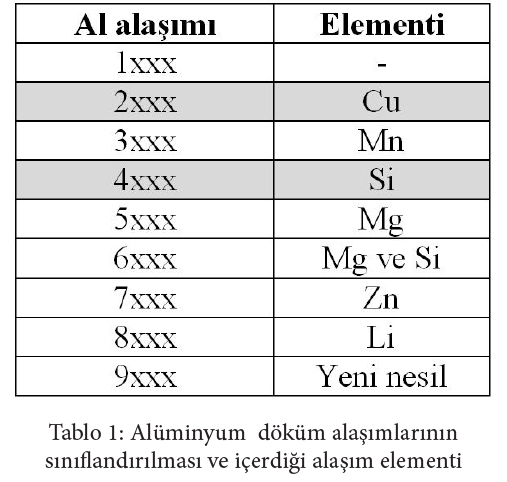
Döküm alüminyum alaşımları arasında yüksek sıcaklık özellikleri en yüksek olan alaşım sınıflarından biri Al-Cu (%7-8 Cu) alaşımlarıdır. Bu alaşımın yüksek sıcaklık aşınma ve dayanım özellikleri, kimyasal bileşime, bakır, nikel, magnezyum ve bazen demir ilavesi ile iyileştirilebilir. Alüminyum alaşımları, döküm yönteminin yanı sıra, toz metalurjisi (Mahle) yöntemiyle de üretilebilmektedir. Bu sayede, daha saf mikro yapı elde etmek ve mekanik özellikleri ve korozyon direncini arttırmak mümkün olmaktadır. Ancak, daha saf bir mikroyapı oluşturmak için hızlı soğutma veya mekanik alaşımla yapılmalıdır. Bu yöntemler ile kafes hatalarını azaltmak ve mikrokristalin fazlar oluşturmak mümkündür [4].
2XXX ve 7XXX serisi aluminyum alaşımları ile karşılaştırıldığında Al-Li-X alaşımları düşük yoğunluk, yüksek elastisite modülü, mükemmel yorulma dayanımı ve iyi tokluk özelliklerinden dolayı tercih edilmektedir [5]. Alüminyum lityum alaşımları da, 2XXX, 6XXX ve 7XXX alaşımları gibi, çökelme sertleşmesi ısıl işlemi uygulanabilmektedir [5]. Ancak, çökelme sertleşmesi uygulanması sonucu oluşan fazların yüksek sıcaklıklarda çözünmesi sonucu dayanım azalmaktadır. Bu nedenle, alüminyum lityum alaşımları düşük yoğunluk ve iyi dayanım özelliklerine rağmen yüksek sıcaklıklarda yeterli dayanım özellikleri sergileyememektedir.[5]
Otomotiv endüstrisinde çokça kullanılan bir diğer alüminyum alaşım grubu da Al-Cu (2XXX) serisi alüminyum alaşımlarıdır. Bu alaşımlarda temel alaşım elementi bakır, ikinci element ise magnezyumdur. 2XXX serisi alüminyum alaşımları döküm yöntemi ile üretilmektedir. 2XXX serisi alüminyum alaşımları yüksek dayanım değerlerine sahiptir, ancak korozyon direnci diğer alüminyum alaşımları ile karşılaştırıldığında düşüktür. Bu sebeple yüksek sıcaklık uygulamalarında kullanılması mümkün değildir [2]. Yüksek sıcaklık uygulamalarında kullanılmak üzere birçok T/M ile üretilmiş hızlı soğutulmuş aluminyum alaşımı araştırılmış belki de bunlar arasından en çok gelecek vaat eden alaşım Al-Fe-Ce alaşımları içinden CU78 (Ce içerikli) ve CZ42 (Zr içerikli) olarak belirlenmiştir. Spear ve arkadaşlarının çalışmalarında bu alaşımlar 315°C’ye kadar yüksek akma dayanımı göstermektedir. Bu alaşımların korozon deneyinde %3.5 NaCl çözeltisi içinde 275 Mpa gerilme altında 180 gün sonunda bir kırılma olmadığı gözlemlenmiştir. Yüksek sıcaklık uygulamalarında kullanılmak üzere gelecek vaat eden bir diğer alaşım grubu, hızlı soğutma ve toz metalurjisi yöntemleri ile üretilmiş Al-Fe-Si–V alaşımlarıdır [5].
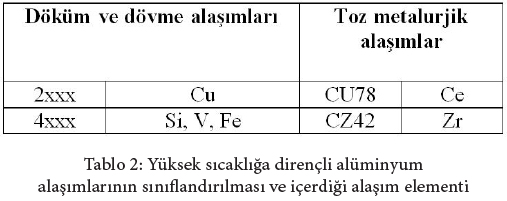
Al-Fe-X sisteminin bir üyesi olan Al-Fe-Ce alaşımı sistemi yüksek sıcaklık uygulamalarında kullanılmaktadır. Bu alaşımlardan biri olan, Al-8Fe-Ce alaşımı içerisindeki matriks içerisinde uniform dağılmış ince Al-Fe-Ce fazı dayanımı artırmaktadır. Şekil 1’de Al96Fe3Ce1 (US5579822A) alaşımı içerisindeki ince taneli Al-Fe-Ce fazı görülmektedir. [6]. Bu mikroyapı hücresel üç farklı yapı içermektedir. Alüminyum katı çözeltisi matrisi içerisinde küresel formda nanometre seviyesinde Al-Fe-Ce çökeltileri ve bunun etrafında Al-Al3Fe lamelli ötektik yapı ile çevrelenmiştir. Yapıda çok yüksek mikrosertlik bölgeleri (2 Gpa) mevcuttur. Ce ilavesi yapıda yüksek sıcaklıklarda, sertlik artışında önemli bir etkiye sahiptir [7].
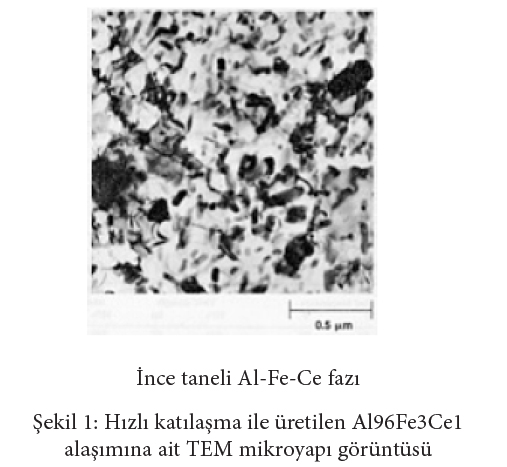
Yüksek sıcaklıkta kullanılan Al alaşımlarının en önemlilerinden biriside Al-Si alaşımlarıdır. Silisyum sıvı alüminyumun akışkanlığını arttırır. Silisyumun ilavesi ile alaşımın mukavemeti de artar. %5 Silisyumlu malzeme ince, karmaşık şekilli ve işlenebilme kabiliyeti az , korozyon direnci yüksek olan parçalarda kullanılmaktadır. %5‘den fazla silisyum içeren alaşımlarda ise iri köşeli olan silisyum kristallerinin oluşumunu önlemek amacı ile sıvı halde sodyum ile karıştırıp modifiye edilmesi en önemli işlemdir. %13 silisyumlu alaşımlarda ise korozyona karşı direnci ve termal şok direnci Al–Cu alaşımından daha fazla olduğundan denizcilik ve otomotiv endüstrisinde kullanılır.
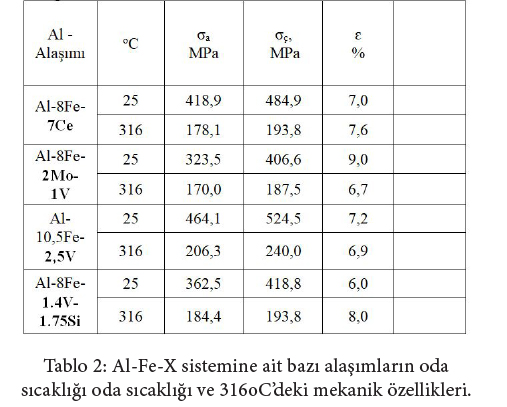
Al-Fe-V-Si alaşımlarında, ß-Al13FeSi fazı iğnesel morfolojisinden dolayı, gerilme konsantrasyonunu arttırmakta ve tokluğu düşürmektedir. Bu nedenle, kimyasal bileşime vanadyum ilavesi ile ß-Al13FeSi fazı yerine daha ince taneli kübik ß- Al13(Fe,V)3Si fazı oluşmaktadır. Bu fazın oluşumu ile dayanımdan kayıp olmaksızın yüksek sıcaklıklarda kararlılık sağlanmaktadır. Ayrıca, Al13(Fe,V)3Si fazının Al matriks içerisinde üniform dağılması ile yeniden kristalleşme sıcaklığı artmakta ve tane büyümesi de önlenmektedir. Alaşımın özellikleri ß-Al13(Fe,V)3Si fazının matriks içerisinde dağılımına göre değişmektedir. Şekil 2’de bu fazları matriks içerisinde dağılımları görülmektedir. Buna göre, Şekil 2a’da 1 ile gösterilmiş kısımlar ß fazını 2 ile gösterilmiş kısımlar ise ß fazını göstermektedir. Şekil 2.b’ de ise 2 ile gösterilmiş kısımlar iğnesel morfolojideki ß fazını, 3 ile gösterilmiş kısımlar ise V zengin bölgeleri göstermektedir [6].
Tablo 2 incelendiğinde, Al-Fe-X alaşımları içinde Al- Fe-Si-V alaşımlarının mekanik özelliklerinin Al-Fe-Ce alaşımına göre daha iyi olduğu, bu nedenle yüksek sıcaklıklarda kullanım için en uygun adaylardan biri Al- Fe-Si-V alaşımları olarak görünmektedir [6,8].
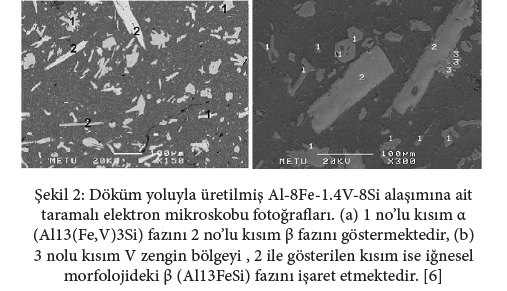
Silisyum miktarı %7–12 aralığında olan Al–Si alaşımları yüksek mukavemet gerektiren yüksek sıcaklıkta aşınma direnci istenen uygulamalarda kullanılmaktadır. Mekanik özellikler, alaşımın bileşiminden çok silisyum içeren fazın şekli ve dağılımına bağlıdır. Küçük ve yuvarlak primer faz (veya ötektik yapı) yüksek mukavemet ve süneklik verir. İğne şeklindeki silisyumlu faz çekme mukavemeti arttırmakla beraber süneklik, darbe ve yorulma mukavemetini düşürmektedir. Silisyum ilavesi ile dökümün akışkanlık ve korozyon direnci artar. Tane küçültme ve modifikasyon işlemleri ile iyi işlenebilme sağlanabilir. Ayrıca sıcak yırtılma eğilimini azaltmaktadır. Silisyum ve bakır beraberce alaşımlandırma amacı ile kullanılabilmektedir. %6 Si, %5 Cu alaşımının kaynak kabiliyeti iyidir. %9 Si %4 Cu alaşımı ise sızdırmazlık isteyen yerlerde tercih edilmektedir. Al–Si alaşımlarında da Fe ve Mg varsa süneklik düşmektedir. Bu alaşım sisteminde müsaade edilen empürite element yüzdeleri %0,5 Zn, % 0,6 Cu, %1,3 Fe , %0,3 Mg olmaktadır. Silisyum, alaşım hazırlamada Al-%13–22 Si ön alaşımı şeklinde ilave edilmektedir. Özel bazı piston alaşımları %25 ‘e varan silisyum içermektedirler. [8,9] Al-Si alaşımlarının mikroyapısında primer Si ve Al-Si esaslı fazlar oluşturarak, yüksek sıcaklık mekanik özelliklerini arttırmak için ısıl işlemler uygulanır. Uygulanan ısıl işlemlerin en yaygınları; T4, T5 ve T7 sıcaklık kodlarıyla adlandırılan ısıl işlem (yaşlandırma) türleridir.
Geleneksel alüminyum alaşımlarının; yüksek sıcaklıklarda mekanik özellikleri olumsuz etkilenmektedir ve pistonların çalışma sıcaklığı olan 250-300oC civarında hasara sebebiyet vermektedir. Bu durum, alüminyum alaşımlarının geliştirilmesi için yeni mikroyapı tasarımı, üretim yöntemi, ısıl işlem yaklaşımların ortaya atılmasına ve çalışmaların artmasına neden olmuştur [10,11].
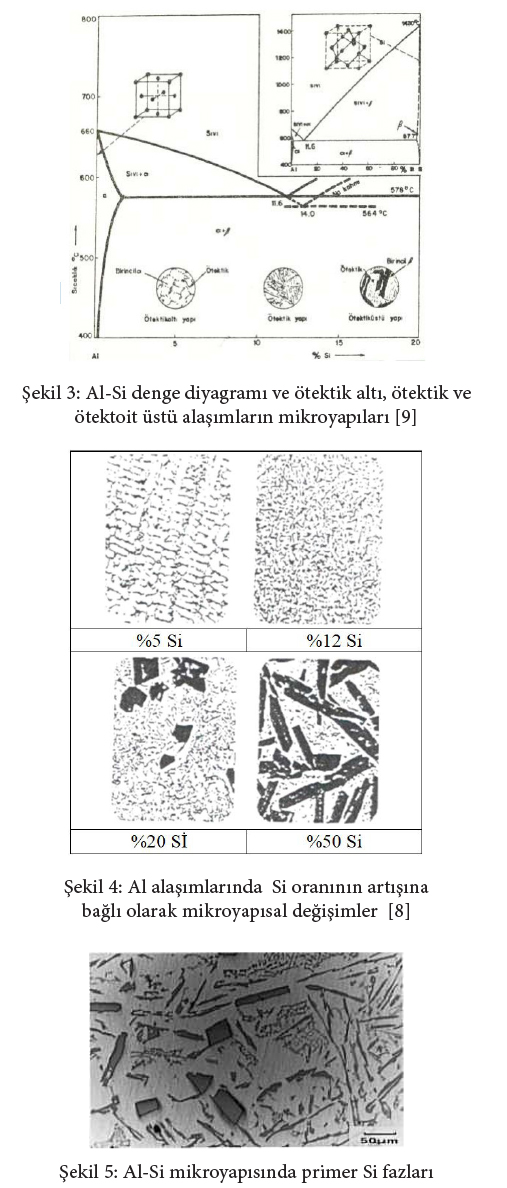
Yüksek sıcaklıklarda mekanik özelliklerin iyileşmesinde alüminyum alaşımları konusunda çalışmalar yürüten kurumlardan bir taneside NASA (National Aeronautics and Space Administration – Ulusal Havacılık ve Uzay Dairesi)’dır. NASA yüksek sıcaklıklarda kullanılmak üzere alüminyum-silisyum alaşımı geliştirmiştir. Al-Si yüksek sıcaklıklarda latis uyumsuzlukları sebebiyle yüksek sıcaklıklarda kullanım yeri bulamamıştır. Mukavemeti arttırmak için Al-Si alaşımına maaliyeti düşük sert takviye ilave etme fikri olan ‘’alüminyum metal matriksli kompozit’’ teknolojisi olarak bilinen yöntem ortaya atılmıştır[2].
2.ALÜMİNYUM PİSTON ALAŞIMLARI, PİSTONLARIN ÇALIŞMA ŞARTLARI VE HASARLARI
Bir otomobil motorunda yakıt-hava karışımı silindir içinde ateşlendiğinde genişleyen gazlar pistonu aşağıya iterek piston koluna (biyel) bağlı olan krank milini döndürmektedir. Bir buhar makinasında, yüksek basınçlı buhar silindirin bir ucundan girerek pistonu itmektedir. Bu ilerleme hareketi pistona bağlı krank-biyel mekanizması yardımıyla dönme hareketine çevrilmektedir. Bir pompada piston elle veya bir makina ile hareket ettirilerek su veya sıvıların hareket ettirilmesinde veya yükseğe basılmasında kullanılmaktadır. Bir kompresörde makina veya motor pistonu çalıştırarak silindir içindeki hava veya diğer gazların daha yüksek bir basınçta sıkıştırılmasını sağlamaktadır.
Piston silindir kapağı ile birlikte yanma odasını oluşturmaktadır. Yanma zamanında meydana gelen, yüksek sıcaklığa dayanabilmeli ve bu ısı karşısında şekil değiştirmeden, sıkışmadan görevine devam edebilmelidir. Ayrıca piston yanma zamanında meydana gelen yüksek basınca da dayanabilmeli, uzun süre ısı ve basınç altında normal şeklini koruyabilmelidir. [10]
Piston, üzerine gelen gaz ve kendi kütlesinden doğan atalet kuvvetlerini krank miline iletmektedir. Gazlar tarafından piston yüzeyine verilen ısının büyük bir kısmı segman bölgesinde segmanlar üzerinden silindir yüzeylerine ve oradan da soğutucu akışkana geçmektedir. Bu ısı akışı sırasında yüksek sıcaklıklar ve sıcaklık farkları dolayısıyla büyük termal ve iç gerilmeler meydana gelmemelidir [11].
Otomobillerde kullanılan pistonlarda ilk olarak gri dökme demirleri, yumuşak dökme çelik, krom nikelli çelik pistonlar takip etmiştir. Günümüzde ise yaygın olarak alüminyum alaşımı pistonlar kullanılmaktadır. Alüminyum alaşımı pistonlar ısı iletme yeteneği daha yüksek olduğundan diğer pistonlara göre daha iyi soğutulabilmektedir. Düşük yoğunlukları nedeniyle atalet kuvvetleri de düşmektedir [10]. Piston malzemesi olarak alüminyum alaşımları kullanılmakta olup, alaşım elementi olarak silisyum, demir, bakır, mangan, manganez, nikel, çinko, titanyum, krom ve kurşun gibi madenler ilave edilmektedir. Bu elementlerin değişik oranlarda alüminyuma ilave edilmesiyle alüminyum alaşımı darbelere, ısıya, korozyona ve aşınmaya karşı dayanımı artırılmış olmaktadır [11].
Çalışma şartları göz önüne alındığında, düşük yoğunluk, yüksek dayanım, yüksek ısı iletkenliği, düşük ısı genleşmesi, aşınmaya karşı yüksek oranda dayanıklılık istendiğinden aranan özelliklerin birçoğu alüminyum-silisyum alaşımı ile sağlanabilmektedir [1].
3.ALÜMİNYUM PİSTON ALAŞIMLARI, PİSTONLARDA KARŞILAŞILAN HASARLAR
Pistonların tabanı 40-60 bar dolayında yanma basıncı altında çalışmaktadır. Bu basınç zamanla pistonun ve piminin deforme olmasına neden olur. Yanma odasında 2500oC’ye kadar sıcaklık oluşmaktadır. Benzinli motor pistonunda motor tam yükte iken piston eteğinde 120oC, piston başında yaklaşık 280oC, piston tabanının merkezinde ise 300oC’lik bir ısı oluşmaktadır. Dizel motorlarda, sıkıştırma esnasında yani ateşleme konumunda iken bu sıcaklıklar 500oC’ye kadar çıkabilmektedir [11,1].
Kırık piston segmanları, piston kafalarındaki yanmış yada ergimiş bölgeler ve piston eteklerinin sıyrılması, en sık görülen üç piston hasarı çeşitlerindendir. Kırık segman hataları motor vuruntusundan meydana gelir. İçten yanmalı motorlarda meydana gelen vuruntu, yanma odası içerisinde oluşan yanma safhalarının istenen düzeyde gerçekleşmesini engelleyerek motor veriminin düşmesine, başta yanma odası parçaları olan piston, supap, sekman, silindir kapağı ve silindir yüzeyi üzerinde çeşitli hasarlara sebep olmaktadır. Bu tip hatalar sıcaklık farklarından meydana gelen hatalardır [1].
Piston kafası, merkez boyunca yada kenarlar boyunca eriyebilmektedir. Çok kez, ergiyik malzeme, pistonun kafası üzerinde tekrar dibe çökmektedir. Ön ateşleme, piston kafasının ergimesinin yada yanmasının olası nedenidir. Aşırı ısınmış motor, çok yüksek motor vuruntusu sıcaklık farklarını ve basıncı arttırmaktadır. Bu da piston malzemelerinin çalışamaz duruma gelmesine sebep olmaktadır. Hataların giderilmesi çalışmaları devam ederken, hatalara karşı malzemelerin dayanımları konusunda çalışmalar getirilmeye çalışılmaktadır. Al-Si alaşımlarının kullanımı bu hataları minimize etme çabalarının sonucudur. Silisyum , alaşım hazırlamada Al - %13 – 22 Si ön alaşımı şeklinde ilave edilir. Özel bazı piston alaşımları %25 ‘e varan silisyum içermektedirler[1].
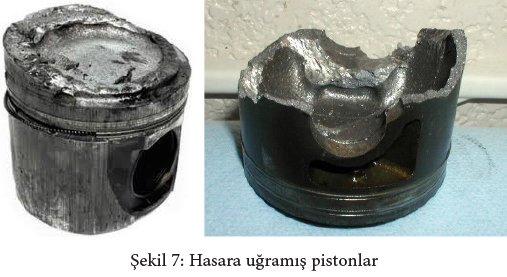
4. ALÜMİNYUM ALAŞIMLARINA UYGULANAN ISIL İŞLEMLER
Düşük sıcaklıklarda mekanik özelliklerini koruması alüminyumun bir başka üstün özelliğidir. Elde edilen sonuçların avantajları nedeniyle özellikle ısıl işlem uygulamaları öne çıkmaktadır. Al alaşımlarına farklı amaçlar için çok farklı ısıl işlemler uygulanabilmektedir. Bunların başında temperleme, su verme ve yaşlandırma gelmektedir. Alüminyum alaşımları için ısıl işlem genellikle, çökelme sertleşmesi gösterebilen işlenmiş alaşımların mukavemetini ve sertliğini arttırmak için uygulanan işlemlerle sınırlanmaktadır. Alüminyum alaşımlarının mukavemetinin arttırılması amacıyla uygulanan çökelti oluşturma ısıl işlemi; çözeltiye alma, fazların çözülmesi (katı çözeltinin oluşturulması), su verme; aşırı doymuş yapının oluşturulması, yaşlanma; çözünen atomların oda sıcaklığında veya daha yüksek sıcaklıklarda çökelmesi (çökelme sertleşmesi) olmak üzere üç basamaktan oluşmaktadır. Diğer yandan Al alaşımlarına ısıl işlem uygulanabilmesi ya da daha doğrusu başarılı bir ısıl işlem (özellikle yaşlandırma ısıl işlemi) uygulanabilmesi için özellikle Cu, Mg, Fe, Mn, Sn ve Zn elementlerinin varlığının gerekliliği vurgulanmaktadır. Prof. Dr. Ali Kalkanlı’nın çalışmaları alaşım elementlerinin önemli olduğu görüşünü desteklemektedir. Çünkü bu elementler ısıl işlem sonucunda çökeltiler (Mg2Si, Mg3Mn2Al18, AlFeSi, AlCuMgSi, Al2Cu vb.) oluşturmak için gerekmektedir. Oluşturulan bu çökeltiler ise dayanımı ve sertliği geliştirmektedir [15]. Aşırı doymuş bir katı fazdan yeni bir fazın meydana gelmesi olayına teknolojide “yaşlanma olayı” denilmektedir. Aşırı doymuş atomlar belli kristal düzlemleri boyunca toplanma eğilimi göstermektedirler. Bu ergiyikteki Cu atomlarını toplanması (ergiyen atomlar) diğer taraftan Cu yoğunluğunu azaltmakta, daha az aşırı doymuş ve dolayısıyla daha kararlı bir kristal yapısı oluşturmaktadır. Bu durumdaki bakır atomları henüz fark edilecek bir faz yapmamışlardır, hududun iki tarafındaki iki yapı arasında atom bağlaçları vardır. Dislokasyon hareketinin bu düzensiz alanlardan geçmesi zordur. Bu sebeple metal sertleşmekte dolayısıyla gerilmeler altında deformasyona daha dayanıklı olmaktadır.
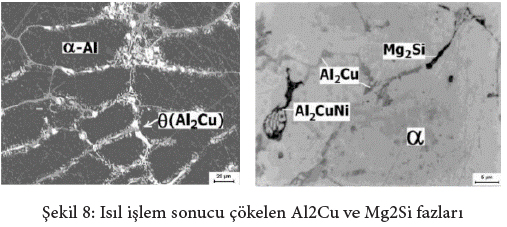
1938’de Preston ve Guinier birbirlerinden habersiz olarak transmisyon latis çökelmesinin bir önceki kademesini bulmuşlardır. Difüze olmuş değişmelerin matriks bölgesinde olduğunu göstermişlerdir. Çözünen atomlar, çözücü atomlardan boyut yönünden önemli miktarda farklı ise matriks latisi distarsiona uğramaktadır. Fakat yeni ve kesin olmayan kristal yapıları bu kademede de zenginleşen bölgelerde birleşememektedir. Bu bölgelere “GP” zonu denilmektedir. [15,16]
Alüminyum ısıl işlemleri; ısıl işlemden sonra deformasyonla sertleştirilen veya sertleştirilemeyen ürünler için geçerli olan T sembolleri ile gösterilir. [6,16,17,18]
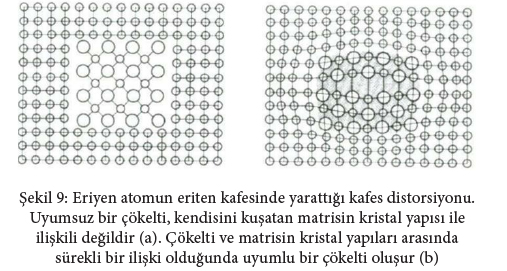
• T1: Yüksek sıcaklıkta bir şekillendirme işleminden soğutulup oldukça dengeli bir duruma yaşlandırılmış malzemeyi göstermektedir. Döküm veya ekstrüzyon gibi yüksek sıcaklıkta bir şekillendirme işleminden sonra soğutma hızları dayanım yükselmesi sağlamaktadır.
• T2: Tavlanmış malzemeyi göstermektedir. Boyutsal kararlılık ve şekillendirme özelliklerini yükseltmek üzere tavlanan ürünler için kullanılmaktadır. Yalnız döküm ürünleri için geçerli olmaktadır.
• T3: Katı çözeltiye alma ısıl işleminden sonra soğuk işlenmiş malzemeyi belirtmektedir. Sadece döküm ürünler için geçerli olmaktadır. Dayanımı arttırmak üzere soğuk işenmiş veya haddelenmiş ürünler için kullanılmaktadır.
• T4: Katı çözeltiye alma işleminden geçirilmiş ve oldukça kararlı bir durumda bekletilmiş malzemeyi göstermektedir. Katı çözeltiye alma işleminden sonra soğuk işlenmeyen veya haddelenmiş ürünler için kullanılmaktadır.
• T5: Yüksek sıcaklıkta bir şekillendirme işleminden sonra suni yaşlanmayı belirtmek için kullanılmaktadır. Döküm veya ekstrüzyon gibi yüksek sıcaklıkta bir şekillendirme işleminden sonra soğutup mekanik özellikleri, boyutsal kararlılığı veya her ikisini birden arttırmak için suni yaşlandırılan ürünler için kullanılmaktadır.
• T6: Katı çözeltiye alma ısıl işleminden sonra suni yaşlanmayı belirtmek için kullanılmaktadır. T6 işareti verilen malzemelere katı çözeltiye alma ısıl işleminden sonra soğuk işlem yapılmamaktadır.
• T7: Katı ergiyik işleminden sonra özel bir karakteristiğin kontrolü için azami dayanımın ötesine dengelenmiş olan ürünler için kullanılmaktadır.
• T8: Katı çözeltiye alma işleminden geçirilmiş, sonra soğuk işlenmiş ve daha onrada suni yaşlanmış malzemeyi belirtmektedir. Dayanımı arttırmak için soğuk işlenmiş malzemede, soğuk işlem etkilerinin şartnamelerde dikkate alındığı ürünler için kullanılmaktadır.
• T9: Katı çözeltiye alma ısıl işleminden sonra suni yaşlandırma ve daha sonrada soğuk işlem yapılmış malzemeyi göstermektedir. Dayanımı arttırmak üzere soğuk işlenen ürünler için kullanılmaktadır.
• T10: Yüksek sıcaklıkta bir şekillendirme işleminden sonra suni yaşlanmayı ve daha sonrada soğuk işlenmeyi belirtmektedir. Döküm veya ekstrüzyon gibi yüksek sıcaklıkta bir şekillendirme işleminden sonra soğutulup suni yaşlandırılan ve daha sonra da dayanımı daha çok arttırmak üzere soğuk işlenen ürünler için kullanılmaktadır. [6,17]
Alaşımlara alaşım elementi ilavesi ile mukavemet arttırmak mümkün olmaktadır. Bakır, magnezyum ile birlikte bileşik yaparak yaşlanma ile sertleştirme özelliklerini vermek için kullanılmaktadır. Bakırın magnezyum ile yaptığı tepkime sonucu oluşan bileşik, alüminyum matrisi içinde yüksek sıcaklıkta kararlı bölgeler oluşturmakta ve mekanik özellikleri etkilemektedir. Alüminyum matris içerisinde Al2Cu (0) fazını oluşturan bakır elementi kararlı bir faz durumundadır. Cu ile birlikte etkili olan elementlerden biri ise magnezyumdur. Cu ile Mg ‘un oluşturduğu faz ile birlikte mukavemet artmaktadır. Al2CuMg (S) ve Al2Cu fazlarının oluştuğu latislerde sadece Al2Cu fazının oluştuğu latislere göre yüksek mukavemetler görülmektedir [15,16].
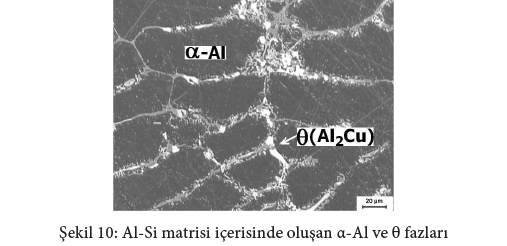
Alüminyum silisyum alaşımlarının mukavemeti tane sınırlarında bulunan çökelmiş fazlarla etkilenmektedir. Al-Si alaşımına titanyum, vandayum ve zirkonyum ilavesi Al3X (X=Ti, V, Zr) yapılarının parametrelerini değiştirerek mekanik özelliklerine etki etmesi için kullanılmaktadır. Alüminyum matrisi ve Al3X bileşiklerinin YMK kristal yapısına parçacıkları birbirine uyumlu yapı oluşuturmaktadır. Bu da alaşımın ergime noktasına yakın sıcaklıklarda mukavemeti yüksek derecelere çıkarmaktadır [14,15].
Al-Si alaşımı için Co ve Ni (Ni, Co)3Al4 fazını oluşturmaktadır. Bu faz sertlik ve yüksek sıcaklık mekanik özelliklerini iyileştirmektedir. Alüminyum alaşımına Co ve Ni elementlerinin ilavesi ile matris içerisinde oluşan Co-Ni fazları Şekil 11’da gösterilmiştir [19].
Geleneksel alüminyum alaşımlarından olan A319 alaşımına göre, Co-Ni fazı bulunduran Al-Si alaşımlarında mukavemet değerleri yapılan araştırmalar sonucu kanıtlanmıştır. A319 alaşımının mukavemeti 270oC’lerin üzerinde çok hızlı düşmekte iken Co-Ni fazlı yapılar kararlılığını 400oC’nin üzerine kadar sağlamıştır [18]. Şekil 12’de mukavemet değerleri gösterilmiştir [19].
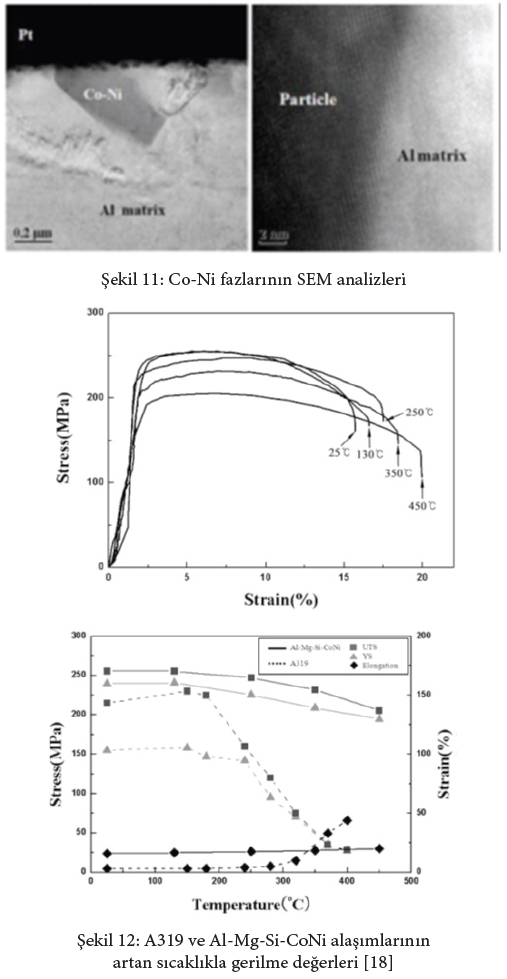
4.GELENEKSEL ALÜMİNYUM PİSTON ALAŞIMLARI VE NASA 398 ALÜMİNYUM ALAŞIMI
Bugüne kadar Al-Si alaşımları, 235oC sıcaklıklarda kullanılması için amaçlandı. Bu sıcaklıkların üzerinde, alaşımların mikroyapı mekanizmalarının mukavemeti kararsız durum sergilemektedir. Hızlı kabalaşma ve çözülme yüksek sıcaklık uygulamaları için istenmeyen mikroyapıya sahip alaşım elde edilmesine sebep olmaktadır. Bu tür alaşımlar, alüminyumun katı çözeltilerinin latisleri ve çökelme sertleşmesi parçacıkları arasında uyum eksikliğinden dolayı, yüksek sıcaklıklardaki pratik uygulamalarda çok az kullanım alanı bulmaktadır. Genel olarak, büyük orandaki latis uyumsuzlukları, istenmeyen mikroyapıların oluşumuna katkıda bulunmaktadır ve alaşımların yüksek sıcaklıklarda yüksek mekanik özellikler gösterememesine sebep olmaktadır. [2]
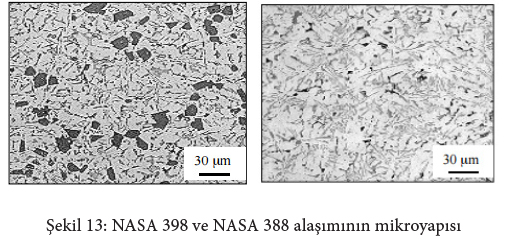
NASA’nın geliştirdiği yeni alüminyum alaşımı, düşük maaliyetli yüksek sıcaklığa dayanıklı döküm bişeşimleri; pistonlar, silindir kafaları, rod bağlantıları, aktüatörler, fren parçaları, rotorlar gibi otomotiv parçalarında kullanılmıştır. NASA 398 alaşımı bulk formda %6 ila %18 silisyım içeriğinde kullanılmıştır. Artan silisyum oranı alaşımın, boyutsal kararlılığını, düşük ısıl genleşme, yüksek yüzey sertliği ve dayanıklı aşınma direnci özelliklerini sağlamıştır. [12]
NASA 398 alüminyum matris içine dağılmış küçük köşeli primer parçacık ihtiva eden yüksek sıcaklıklarda, yüksek mukavemet ve yüksek aşınma direnci özelliklerini sergileyen bir Al-Si alaşımıdır. NASA alaşımları geleneksel döküm kalıpları kullanılarak kum dalıba döküm yöntemiyle ekonomik olarak elde edilebilmektedir ve 260oC’den 500oC’ye kadar kullanılabilmektedir [12].
Yüksek sıcaklıklarda çekme mukavemetini arttırmak için, az miktarda geçiş elementini Al-Si bünyesine ekleyerek Al3x alüminyum matriks yapısında bileşikler meydana getirmek gerekmektedir. Alaşımın ergime noktasına çok yakın sıcaklıklarda mukavemetini korumak için Al3x alaşımındaki gibi YMK bir yapı elde edilmesi için tasarlanmıştır. Latis sisteminde önemli bir uyum elde edilmiştir. Bu uyum; alaşım yüksek sıcaklıklara maruz bırakıldığında, yüksek kararlılık ve yüksek mukavemetli yapılar elde edilmektedir. NASA alaşımları benzersiz kimyasal bileşimlerin performansını maksimuma çıkarmak için ısıl işlem uygulamaktadır [15,12].
NASA 398 alaşımı geleneksel piston alaşımları olan 319, 322, 390 ve 413 alaşımları ile karşılaştırıldığında gösterdiği mekanik özellikler, yüksek sıcaklıklarda kullanım için tercih sebebi olduğunu göstermektedir. NASA 398 alaşımı ve diğer piston alaşımlarının kimyasal kompozisyonu Tablo 3’de gösterilmiştir [15,13].
Geleneksel alaşımlara göre NASA 398’in mukavemeti pistonların eteklerinden başlayarak piston başında yaklaşık olarak 120-270oC sıcaklıklarda yaklaşık iki kat fazla dayanım göstermektedir. Mukavemet değerleri karşılaştırıldığında görülen farklar; piston mekanizmasının merkezinde (yaklaşık 300oC) ve ateşleme anında çıkılan sıcaklıklarda (yaklaşık 400oC) üç kata kadar fazla dayanım göstermesi Şekil 14’de gösterilmiştir.
NASA 398 alaşımının termal, fiziksel ve mekanik özellikleri Tablo 4’te verilmiştir.
Piston çalışma sıcaklıklarında NASA 398’in mukavemet değerleri, alaşımın başarısını kanıtlamıştır. Buna ek olarak döküm ve ısıl işlem maaliyetleri 300 serisi alüminyum alaşımlara göre daha az maaliyetli olmaktadır. NASA alaşımları 730-790oC’lerde geleneksel döküm yöntemleriyle ve ya basınçlı döküm yöntemleriyle üretilebilmektedir. Sıkıştırma döküm yöntemi gibi harici basınç uygulaması bulunan yöntemler ile daha mukavemetli malzemeler dökmek mümkün olmaktadır. NASA alaşımlarının en iyi kullanım aralığı 230-400oC olarak değerlendirilmiştir [13,14].
NASA alaşımlarının kullanım yerlerine ait bilgiler Tablo 3’te verilmiştir. NASA 398 alaşımları genellikle kalıcı kalıba döküm yöntemiyle üretilmektedir ve T5 tipi ısıl işlem uygulanır. T5 ısıl işlemi sıcak şekillendirme sonrası soğutulmuş ve ardından suni yaşlandırma uygulaması yapılmış ısıl işlem türünü ifade eder. Doğal yaşlanma uygulamasına göre suni yaşlanmanın farkı sıcaklıktan dolaydır. Şekil 4’te suni yaşlanma ve doğal yaşlanma sıcaklık farkı ile oluşan fazların farklılıkları gösterilmiştir. T5 ısıl işlemi NASA 398 alaşımının özelliklerini yüksek sıcaklıklarda kararlı kılan en iyi yaşlandırma uygulamasıdır. Şekil 4’te otomotivde kullanılan alaşımlardan, ısıl işlem görmemiş 3 serisi alaşım, T6 ısıl işlemi görmüş 7 serisi alaşım ve T5 ısıl işlemi görmüş NASA alaşımının 100 saat çalışma sonrası mukavemet değerleri karşılaştırılmıştır [20].
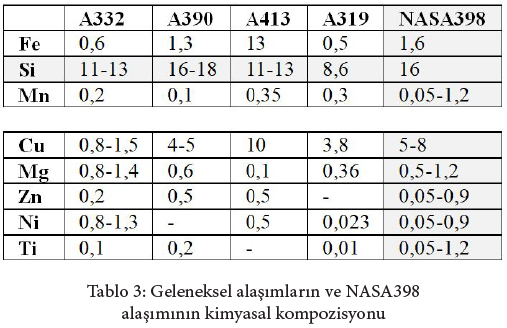
Şekil 5’te T5 uygulanmış NASA alaşımının 400oC sıcaklıkta oda sıcaklığındaki çekme dayanımının %78’ini koruduğu görülmektedir. T5 işlemi görmüş NASA 398 alaşımının termal, fiziksel ve mekanik özellikleri Tablo 3’te verilmiştir. NASA-398, 2,73 g/cm3 yoğunluğuna sahiptir, 620oC sıcaklıkda sıvı faza geçer ve 486 oC’de katılaşmaya başlar [14].
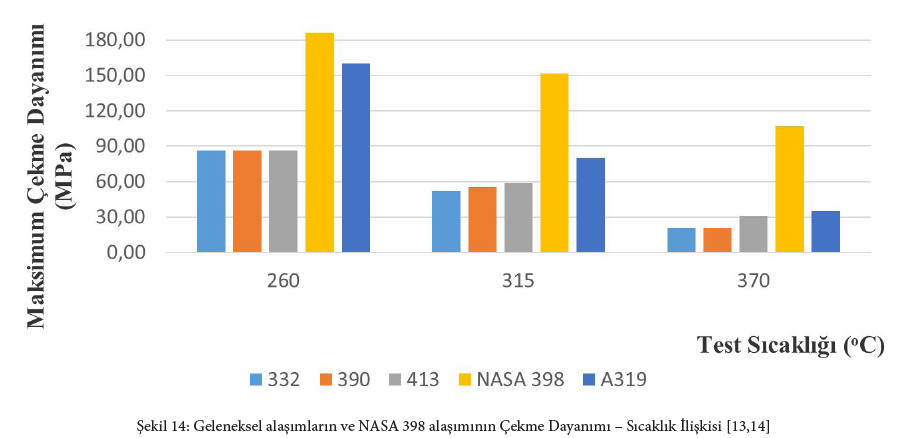
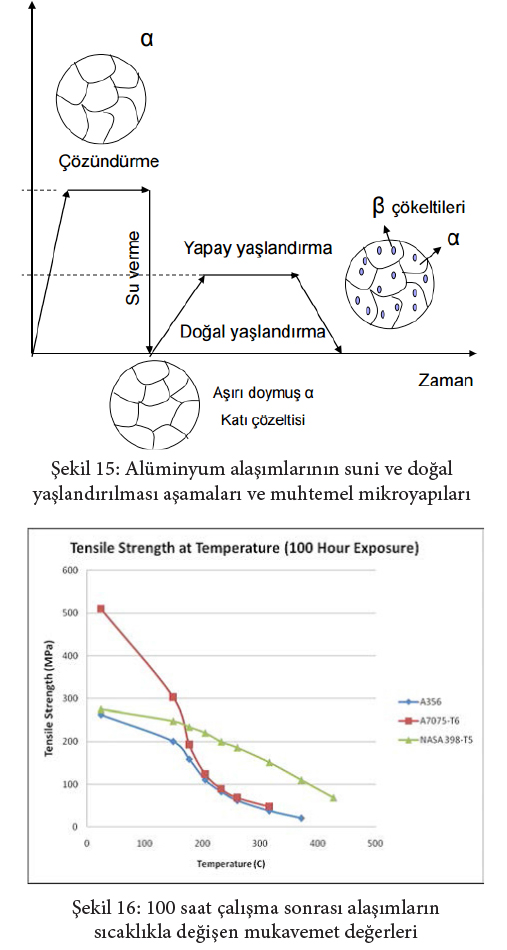
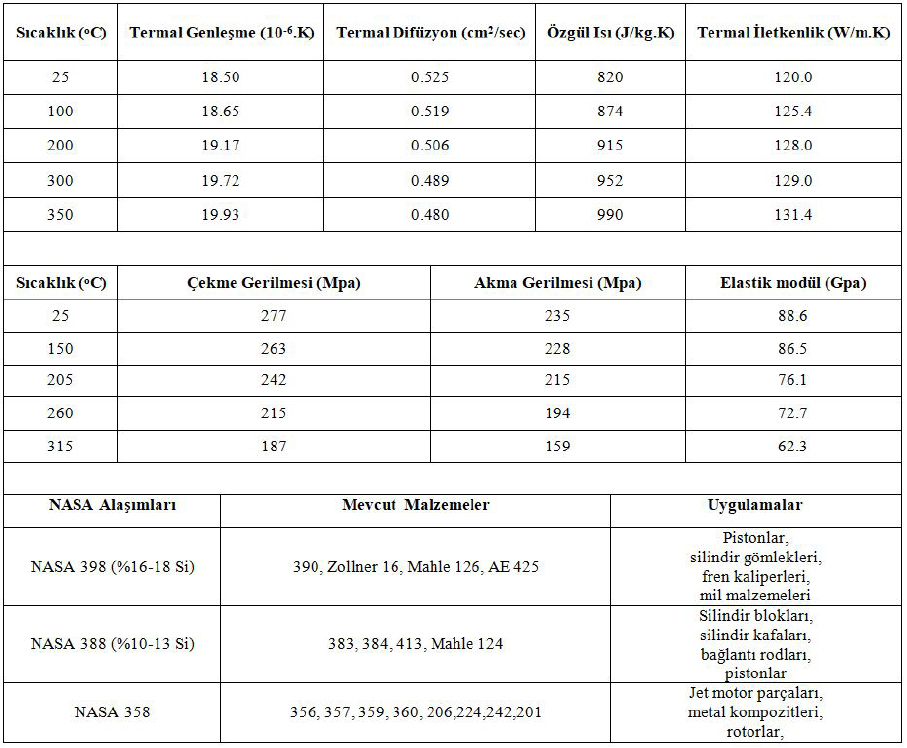
5.SONUÇLAR
Pistonların çalışma şartları göz önüne alındığında, düşük yoğunluk, yüksek dayanım, yüksek ısı iletkenliği, düşük ısı genleşmesi, aşınmaya karşı yüksek oranda dayanıklılık istendiğinden aranan özellikleri sağlayabilmek ve dökme demir türlerinin motor performanslarında dezavantajlara sebep olması yüksek sıcaklığa dirençli alüminyum alaşımlarına ilgiyi arttırmaktadır.
Alüminyum alaşımları dökme demir türleriyle karşılaştırıldığında; düşük aşınma ve yırtılma direnci, daha yüksek maaliyet göstermesine karşın; hafiflik, seri üretimde makine kullanımına uygunluk, yakıt ekonomisi, motorlarda vuruntu azalması, teknolojinin gelişme kapasitesi gibi özelliklerde üstünlük sağladığından otomotiv endüstrisinde kullanımı yaygındır.
Alüminyum alaşımlarının içerisinde ki alaşım elemetleri tanelerarası fazlar oluşturarak dayanımı arttırmaktadır. Oluşan tanelerarası fazlar Al alaşımlarının yüksek sıcaklık kararlılıklarını olumlu yönde etkilemektedir. Si, Fe, Mg, V, Co, Ni elementlerinin tane sınırlarında oluşturduğu fazların etkileri Al-Si, Al-Fe grubu alaşımların yüksek sıcaklıkta daha kararlı malzemeler olmasını sağlamaktadır.
NASA 398 alüminyum matris içine dağılmış küçük köşeli primer parçacık ihtiva etmektedir ve yüksek sıcaklıklarda, yüksek mukavemet ve yüksek aşınma direnci özelliklerini sergilemektedir. Geleneksel alaşımlar olan Mahle 126, Zoller 16 ve A319 alaşımlarının yerine geçebilmesi için tasarlanmıştır.
Ötektiküstü NASA 398 alaşımı ötektik NASA 388 alaşımıyla karşılaştırıldığında yapısındaki primer silisyum parçacıklarının fazla olduğu gözlemlenmiştir. Primer silisyum parçacıklarının fazla olması NASA 398 alaşımının 400oC ’lere çıkıldığında oda sıcaklığındaki mukavemetinin %78’ine saklamasını sağlamıştır.
NASA 398 alaşımı geleneksel piston alaşımı olan A319’dan daha yüksek çekme mukavemetine sahip olduğu gözlemlenmektedir. Piston çalışma sıcaklıklarında A319 alaşımının mukavemeti hızla düşmektedir ancak NASA alaşımı aynı oranda etkilenmemiştir. NASA alaşımı A319’dan 400oC’de yaklaşık üç kat fazla direnç göstermiştir.
NASA 398 alaşımının mekanik özellikleri T5 yaşlandırma türüyle arttırılabilmektedir. Suni yaşlanma sonrası miktarı artan primer fazlar mekanik özellikleri olumlu etkilemektedir.
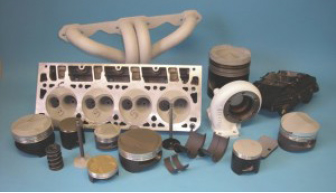
Gelecekte ısıya dirençli bu alaşımlar üzerine yüksek sıcaklıklarda aşınmaya dirençli, termal bariyer görevi yapacak seramik esaslı kaplamalar uygulanarak ısıl ve mekanik direnç artırılarak motor performansının artışına katkı sağlanacaktır. Dizel araçlarda piston kaplamaları ile motor gücü %30 artırılabilmektedir.
KAYNAKLAR
[1] Hazar H., Öner C., ‘’Dizel ve Benzin Motorlarında Vuruntu ve Etkileri’’, Fırat Üniversitesi TEF Makine Eğitimi Bölümü, Elazığ
[2] Joseph R. Davis, ‘’Aluminum and Aluminum Alloys’’, ASM İnternational, 1993
[3] NASA 398 Material Properties Data Sheet, 2011
http://www.pacmaterials.com/data/NASA_398_Data_Sheet.pdf (Erişim Tarihi 03.05.2016)
[4] Sayılgan, S., ‘’Production and Characterization of High Performance AlFe-Si-V Alloys for Elevated Temperature Applications’’, Yüksek Lisans Tezi, O.D.T.Ü Fen Bilimleri Enstitüsü, Ankara, Türkiye, 2009
[5] Spear, K.E., Visco S., Wuchina E.J., Wachsman E.D., ‘’High temperature materials, The Electrochemical Society Interface’’, 48-51, 2006
[6] Darıdereli Y., ‘’Alüminyum Alaşımlarının Mikroyapı, Mekanik Özellikleri ve Aşınma Direncine Yaşlanmanın Etkisi’’, İÜ FBE Yüksek Lisans Tezi, 2010
[7] Laakmann J., "Microstructure Development and Ultramicrohardness of Al-Fe-Ce Solidified Under Free-Fall Conditions", Materials Science & Engineering. A, Structural Materials: Properties, Microstructure and Processing, 173(1-2), 1993, pp. 165-168
[8] Patent No: 4851193, United States Patent, 1989
[9] Koraman E., ‘’Al-Fe-V-Si Alaşımlarının Yüksek Sıcaklık Aşınma Özelliklerinin İncelenmesi’’, İÜ FBE Yüksek Lisans Tezi, 2011
[10] Uyaroğlu A., Yücesu H.S., Çıtak R., ‘’Piston Arızalarının Analizi’’, SAÜ Teknik-Online Dergi, 2010
[11] ‘’Piston Biyel Krank Mekanizması 525MT0281’’, T.C. MEB, 2011, Ankara
[12] Lee J., ‘’Cast Aluminum Alloy For High Temperature Applications’’, The Minerals, Metals and Material Society, 2003
[13] Patent No: 5320688, United States Patent, 1994
[14] NASA 398 Patent Properties
http://www.google.com/patents/US6918970 (Erişim Tarihi 03.05.2016)
[15] Hasırcı H., ‘’Isıl İşlem Şartlarının Ötektik AlSi Döküm Alaşımının Abrasif Aşınma Davranışına Etkileri’’, Gazi Üniversitesi Teknoloji Fakültesi, Metalurji ve Malzeme Mühendisliği, Teknikokullar, Ankara, 2014
[16] Şenaysoy S., Akyüz B., ‘’Effect of Aging on Mechanical Properties and Machining on Aluminum Alloys’’, Bilecik Üniversitesi Fen Bilimleri Dergisi, 2014
[17] R. X. Lİ., ‘’Age-hardening behavior of cast Al–Si base alloy’’, Materials Letters, 2004
[18] Rincon E., ‘’Temperature effects on the tensile properties of cast and heat treated aluminum alloy A319’’, Materials Science and Engineering A, 2009
[19] Choi S., ‘’High Temperature Tensile Deformation Behavior of New Heat Resistant Aluminum Alloy’’, Engineering Procedia, 2011
[20]http://www.clarage.com/docs/flyers/hightemperature-nasa-398-alloy.pdf?sfvrsn=2
[21] Sarath N., Abhijeet M., Dolas D., Significance of Aluminium Alloys in Automobile Engine Components: A Review, International Joutnal of Recent Scientific Research, 2016