Demir ve çelik endüstrisi dünyanın en önemli ve geleneksel açıdan da en eski üretim sektörlerinden biridir. 3.000 yıl kadar önce demir insanların kültür ve uygarlığının bir temeliydi ve o zamanlarda bile cevherden demir elde etmeye çalışılıyordu. O zamandan beri sorun hep aynı olmuştur - demir cevherini, onu ekonomik bir şekilde kullanılır hâle getirmek amacıyla çeşitli teknikler uygulayarak metalik
hâle dönüştürmek.
Demir ve çelik üretiminin başlangıcı ilk çağlara kadar uzanmaktadır. Demirin elde edilmesi muhtemelen milattan 1.000 yıl kadar önce dünyanın çeşitli noktalarında (Batı Afrika, Güneydoğu Avrupa, Güney Hindistan, Çin) eş zamanlı olarak “keşfedildi”. Tarihsel bir öneme ulaşmasından önce bile uygarlıkların demirin nasıl elde edilebileceğini bildikleri ve bu metali işleyerek silahlara, alet ve edevatlara dönüştürebildikleri bir gerçektir.
Demirin kullanılmaya başlanması her hâlükârda bugün Demir Çağı olarak tabir ettiğimiz dönemden (MÖ 800’den itibaren) çok önce başlamış olsa gerekir. Bugün elimizde olan bilgilere göre demir üretimine Anadolu’da ve muhtemelen Kafkaslar’ın kuzeyinde başlanmıştı.
Almanya’da ise demir üretiminin başlangıcı efsanelerin doğduğu çağlara uzanmaktadır; Edda, Wielandsage ve Nibelungen destanı gibi efsaneler ve sagalarda bundan bahsedilmektedir. Bulunan mızrak ve balta parçalarından anlaşıldığına göre, demirin Alman topraklarında
bulunması milattan önceki ilk bin yılın başlarına kadar gitmektedir. Eldeki kanıtlara göre kullanılan ilk demir yeryüzüne katı hâlde düşmüş olan meteorlardan elde edilmişti. Şans, gözlem ve yaratıcılık sonucun da yeterli miktarlarda demir cevheri bulunan yerlerde bunları odun kömürü ile izabe etmek için bol miktarda odun tedariki ile demir elde etme yöntemleri geliştirildi. Gelişme dereceleri farklı olsa da, demir üretimi işlemleri eş zamanlı olarak farklı bölgelerde ilerleme gösterdi. Bu metalin teknik ve ekonomik önemi nedeniyle bilgi ve tecrübeler çoğu kez sır olarak tutuldu ve böylece belirli üretim teknikleri sadece belirli bölgelerle sınırlı kaldı ve ancak uzun bir süre sonra başka yerlere yayılabildi.
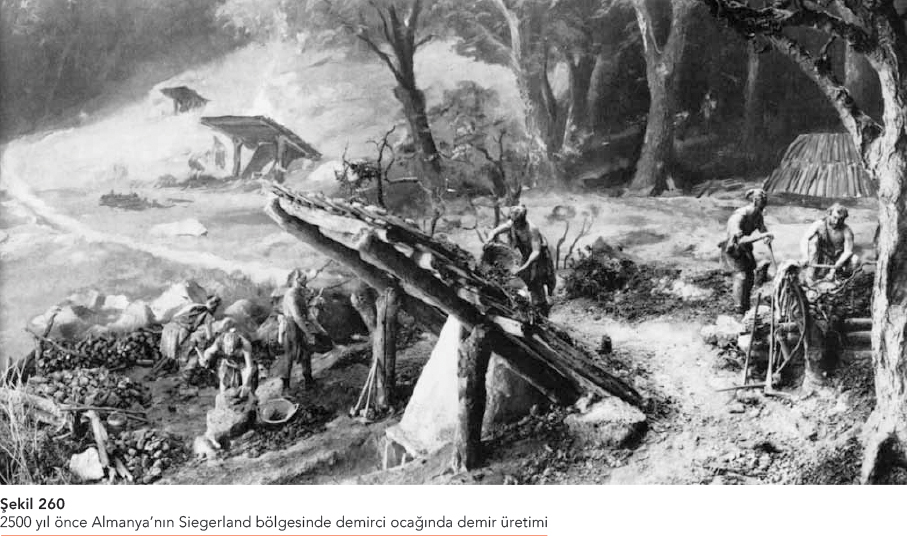
Demir üretiminin gelişme tarihçesi çağlar boyunca demir cevherinin izabe edilmesi için kullanılan farklı ocaklara göre izlenebilir. Buna göre ocakların geçmişten günümüze gelişmesi şu sıralamayı takip etti:
• demirci ocakları
• demirci fırınları
• akışkan yataklı fırınlar ve odun kömürlü yüksek fırınlar
• kok kömürlü yüksek fırınlar
• direkt redüksiyon tesisleri
• izabe tesisleri
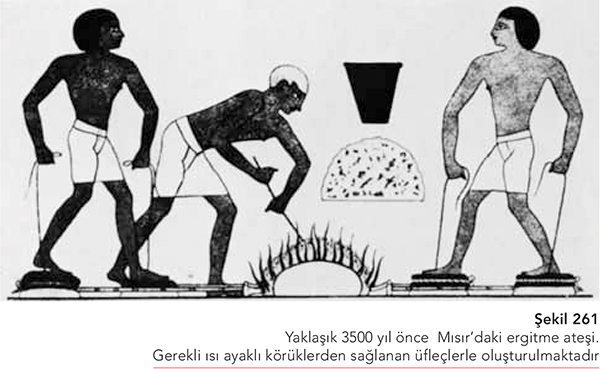
MS 10. yüzyılda su değirmeninin kullanılmaya başlanması demir üretiminde bir devrim yaptı. Suyun yarattığı güç cevher yataklarına yakın olmaktan daha önemli bir hâle geldi. Bunun sonucunda demirin izabe edilmesi için kullanılan ocaklar vadilere taşındı. Su değirmenleri ile çalışan körüklerin daha yüksek hava basınçları üretebilmesi nedeniyle, çok daha büyük fırınların inşa edilmesi mümkün oldu. Bunlar ağırlıkları 100 kilograma ulaşan ve dövülebilir demirden ve kalıntı cüruftan oluşan ve ham demir olarak bilinen külçeler üretmekteydi. Bu yerler “demirci ocakları” olarak biliniyordu (Şekil 262). Ham demir parçaların daha sonra işlenmesi yine su değirmenleri ile çalıştırılan büyük dövme körüklerinin yardımıyla mümkündü.
Isı kullanımının iyileştirilmesi ile birlikte, MS 12. yüzyılda demir cevherinin izabe edilmesine yetecek yüksek erime sıcaklıklarına ulaşılması mümkün oldu. Bu, yüksek fırınların başlangıcıydı. Ortaya çıkan ve son derece akışkan olan ürün başlarda istenmeyen bir ürün olarak addediliyordu ve bu nedenle ona “pig” (domuz) adı verilmişti. Bugün “pik” olarak bildiğimiz demirin adı buradan gelmektedir. Buna rağmen, sıvı metal adıyla anılmaya başlayan sıvı demir modern çelik üretiminde kilit bir rol oynadı.
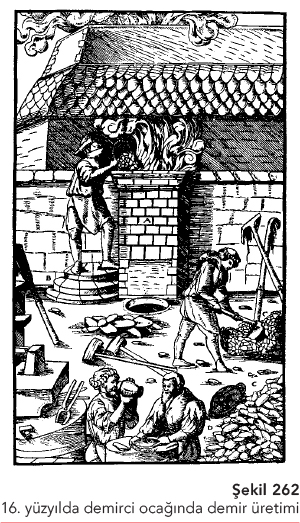
Pik demir o zamanlardaki tabirle ancak “saflaştırıldıktan” veya “rafine edildikten” sonra kullanılabiliyordu.Bugün de bu prosese “rafinasyon” demeye devam etmekteyiz. Bugün olduğu gibi, o zamanlarda da bu işlem karbon ve eser elementlerin ekstra hava akımının sağladığı oksidasyonla yakılmasından ibaretti.
Buna bağlı olarak, uygun bir nihai ürünün üretilmesi için artık iki işleme gerek duyuluyordu - demir cevherlerinin redüksiyon yoluyla sıvı metale dönüştürülmesi ve daha sonra rafine edilmek suretiyle dövülebilir (başka bir deyişle “çekilmiş”) demir, yani çelik elde edilmesi. Rafinasyon işlemi “rafinasyon ateşi” tabir edilen ateşte yapılmaktaydı.
Pik demirin yüksek fırınlarda ticari olarak üretilmesi 14. Yüzyılın başlarına kadar uzanmaktadır. Dökme demir, yaklaşık 1500 yılı itibarıyla dövülmüş alet ve edevat ile sanat eserlerinde (Şekil 263) kullanılmasının yanı sıra, küre, çan, ağırlık ve fırın ızgarası üretiminde de kullanılmaktaydı (Şekil 264).
Odun kaynaklarının zamanla azalması, yüksek fırınlarda kok kömürüne geçilmesine neden oldu. Kömür kullanımı ilk kez 1709’da, o zamanlar dünyanın önde gelen sanayi ülkesi olan Britanya’da, A. Darby tarafından gerçekleştirildi. İlk kok kömürlü yüksek fırın 1796’da Almanya’da, Yukarı Silezya’nın Gleiwitz şehrinde işletilmeye başlandı (Şekil 265). Kok kömürü teknolojisinin ve buhar makinelerinin kullanımının yaygınlaşmasıyla birlikte, yüksek fırınların verimliliği o denli arttı ki, üretim sonrasındaki aşamalarda -yani rafinasyon ocaklarındaki çelik üretiminde ve bunu takip eden şekillendirme operasyonlarında- sıkışıklıklar meydana gelmeye başladı Bunun çözümü 1784’te Britanya’da Henry Cort tarafından icat edilen ve üretim sonrasında haddehane ile birlikte tatbik edilen “karıştırarak yumuşatma” prosesi oldu. Bu yeni teknoloji üretim akışının sıkıntısız gerçekleşmesini sağladığı gibi, demir ve çelik üretiminde odun kömüründen kok kömürüne geçilme aşamasının tamamlanmasını da sağlamış oldu. Burada öncelik kömür veya kok kömüründen çeliğe arzu edilmeyen bir kükürt geçişinden kaçınmaktı, çünkü bunun olması hâ linde çelik sıcak çatlamaya maruz kalıyordu. Cort böylece sıvı metalin sadece oksijen açısından zengin yanıcı gazlarla temasa girdiği bir yansımalı (hava) fırın tasarladı. Rafinasyon işlemi sırasında sıvı metal karıştırılıyor ve hemen yan tarafta bulunan haddehanede işlem görmek üzere katı bir çelik topu hâline getiriliyordu. Şekil 267‘de bu teknolojiyle çalışan, o zamanlara ait bir çelik tesisi gösterilmektedir. İlk sıvı çelik 1740 yılında B. Huntsman adlı bir İngiliz tarafından, hazneli fırın kullanılarak üretilmiştir. Almanya’da bu proses ancak 19. yüzyılın başında kullanılmaya başlandı. Çeliğin hazneli fırında işlenmesi bir ön ergitme operasyonuydu ve burada karbürlenmiş, yani “kaynaştırılmış” çelik ergitiliyor ve sıvı hâle getiriliyordu.
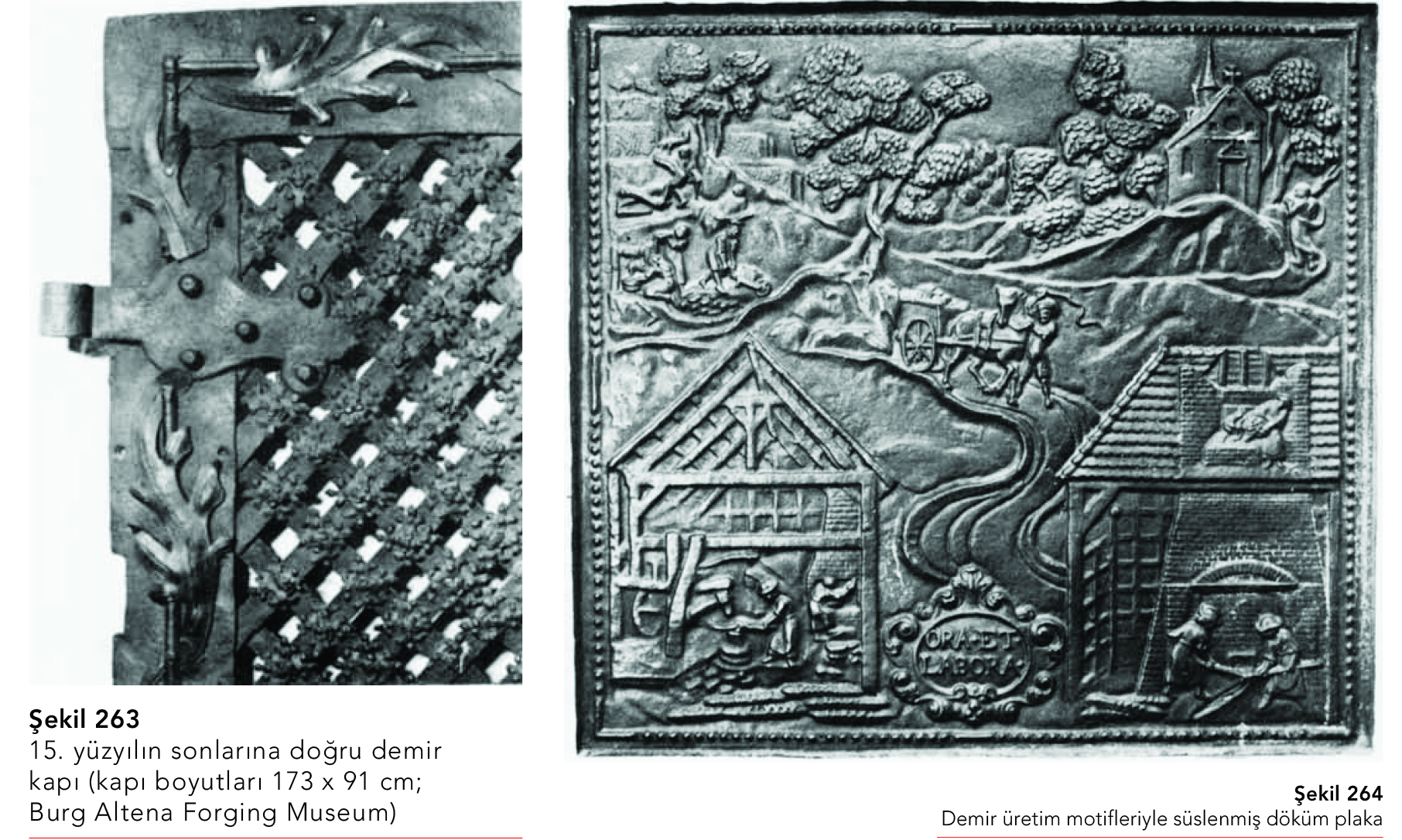
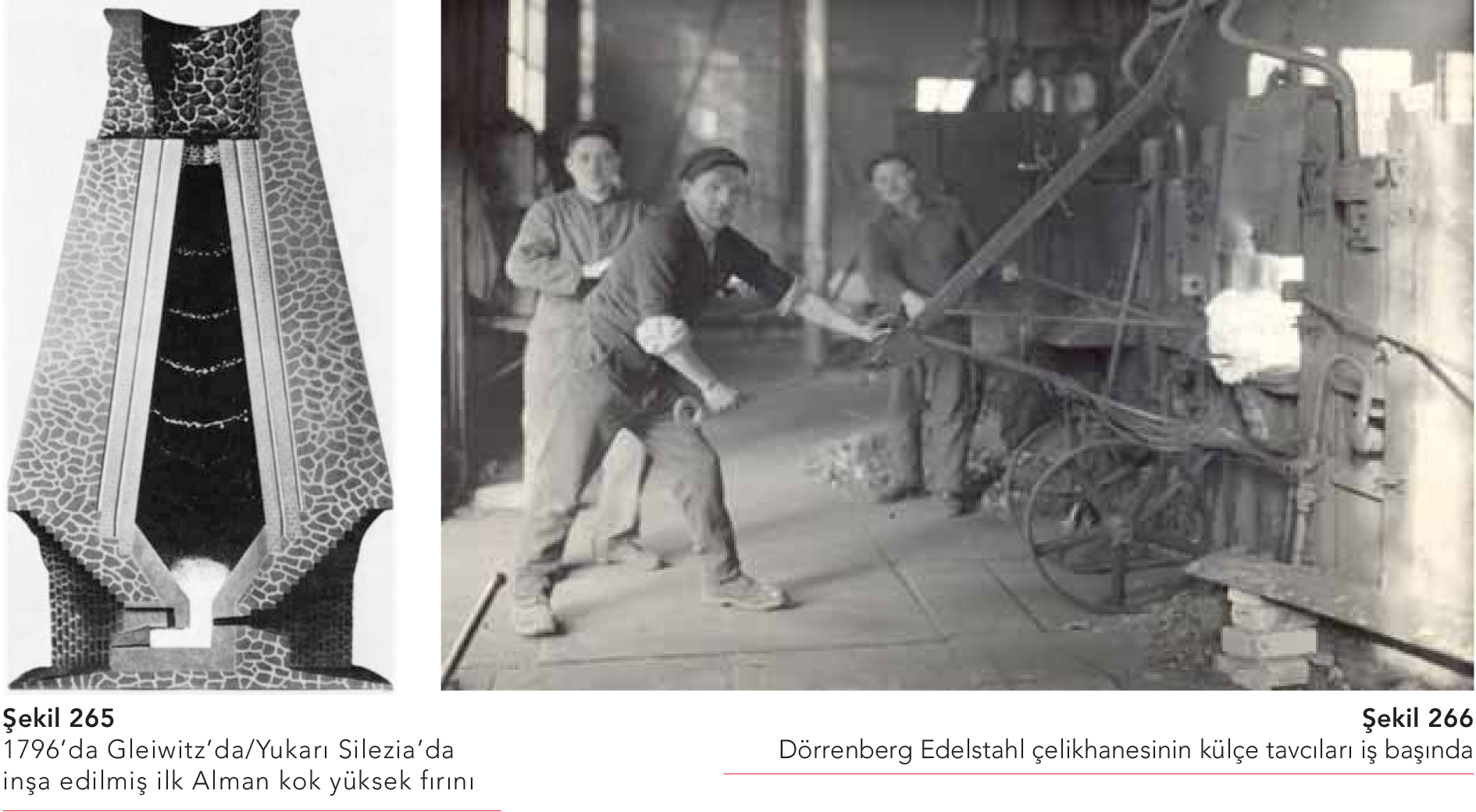
Seri çelik imalatı 1856’da, başka bir İngiliz olan Henry Bessemer tarafından başlatıldı. Kok kömürlü yüksek fırınlarda üretilen sıvı metal miktarlarındaki artış artık verimli bir çelik üretimi tekniği ile desteklenebiliyordu. Bessemer’in bulduğu proseste sıvı metale alttan hava püskürtülüyordu. Bu ise eser elementlerin ekzotermik bir yakılma işlemi ile kolayca ve hızla bertaraf edilmesine olanak tanıyordu. Bunun sonucunda homojen sıvı çelik elde edilebiliyordu. Bessemer prosesi “konverter” adı verilen armut şekilli bir fırında gerçekleştiriliyordu (Şekil 268). Fırındaki refrakter kaplamalarsilisyum asidi içermekteydi. Çelik üretimi açısından bu “asitli” kaplama sadece oldukça nadir olan düşük fosforlu sıvı metalin rafinasyonu için uygundu. 1879’da İngiliz Sidney Gilchrist Thomas yüksek fosforlu sıvı metali “bazik” dolomit kaplamalı bir konverter kullanarak rafine etmeyi başardı (Şekil 269). 1865 civarında çelik üretimine yönelik başka bir etkili proses geliştirildi. Burada sıvı metali ve/veya hurdayı çeliğe dönüştürebilen ve sıcak havayla ısıtılan demirci ocağı tipi fırınlar kullanılıyordu. İngilizce konuşulan bölgelerde açık hazneli fırın olarak bilinen bu teknik Almanya’da onu keşfeden kişilerin adını alarak, Siemens-Martin prosesi olarak ünlü oldu. Elektrik enerjisinin yeterli miktarlarda ve ekonomik fiyatlarla sunulmaya başlanması ile birlikte, çelik üretiminde elektrikle üretilen ısı da kullanılmaya başlandı. Bu yöndeki ilk denemeler 1850’li yıllara kadar uzanmaktadır. Günümüzde elektrik ark ocakları endüstride kendilerine sağlam bir yer edinmiş bulunmaktadır.
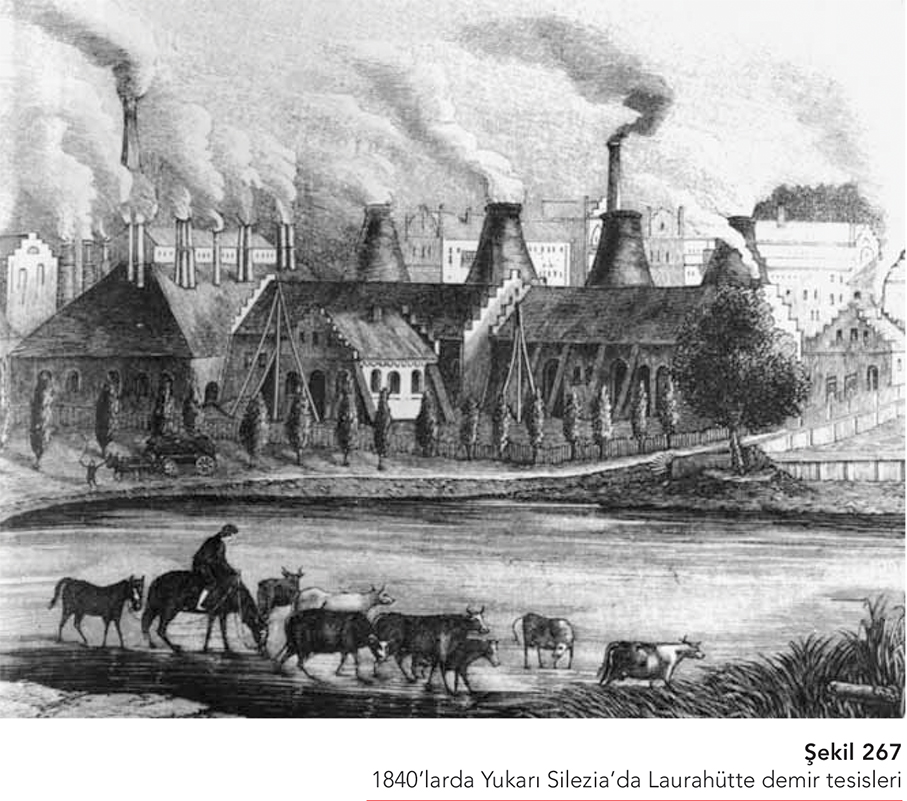
Henry Bessemer yüksek saflıkta oksijen kullanmanın rafinasyon prosesini hızlandırabileceğinin farkındaydı. Ne var ki o dönemde yeterince saf olan oksijen üretmek mümkün olmadı ve dolayısıyla bu fikrin hayata geçirilmesi gerçekçi addedilmedi. Yüksek saflıkta oksijenin hesaplı fiyatlarla üretilmesi ancak 1930’larda mümkün oldu. Üstten oksijen üfleme Thomas ve Bessemer metotlarında kullanılan alttan hava üflemenin yerini alınca, II. Dünya Savaşı’ndan sonra bazik oksijen fırını (BOF) prosesi sektörü kasıp kavurunca, Thomas ve açık hazneli fırın proseslerinin pabucu dama atılmıştı. Bugün Almanya’da çelik tümüyle BOF (ilk BOF tesisi 1957’de devreye sokuldu) ve elektrik ark ocaklarındaüretilmektedir.
Çeliğin sıvı metal ara aşaması olmadan öğretildiği orijinal “direkt” üretim metodu çeşitli direkt redüksiyon proseslerinin çoğalmasıile birlikte tekrar önem kazanmaya başlamaktadır. Sıvı metal yüksek karbon içeriğine sahip olduğundan, üretimi metalürjik anlamda aslında dolambaçlı bir yol teşkil etmektedir 19. yüzyılda çelik üretimindeki gelişmeler haddehane ve dövme teknolojisinde de hızlı bir gelişmeye yol açmıştı. 19. yüzyılın ortalarından itibaren seri çelik üretiminin ortaya çıkması, endüstri toplumunun yol açtığı ve hızla büyümekte olan yeni ürün ihtiyacını karşılayabilecek seri çelik şekillendirme yöntemlerine olan ihtiyacı da körükledi (Şekil 270).Almanya bağlamında buna yönelik kayda değer bir örnek 1861’de inşa edilen ve buharla çalışan yeni gemiler için kardan milleri imal edilmesine olanak veren “Fritz” çekiciydi. Haddehane teknolojilerinde yaşanan önemli gelişmeler sayesinde de levhalardan zırh levhalarına kadar geniş yassı parçalar, raylar, kirişler, tel çubuklar ve de tüpler ve boruların üretimine yönelik sistemler inşa edildi. Performans ve verimliliği daha da artırma ihtiyacının sonucunda 19. yüzyılın sonlarında önce tel çubuk, sonra yassı ürünler için olmak üzere, sürekli haddeleme tesisleri sahneyeçıktı.
Almanya’daki ilk sürekli sıcak şerit haddeleme sistemi 1937’de faaliyete geçti ve ilk sürekli sıcak şerit haddehanesi 1953’te inşa edildi. Çelik üretimindeki güçlü büyüme ilk olarak yaklaşık 150 yıl önce ortaya çıkan çok sayıda teknolojik icat ve gelişmenin sonucunda meydana geldi. Ancak bu tarihsel gelişmelerin teknolojik açıdan önem taşıyan diğer gelişmelerin bağlamında değerlendirilmesi gerekiyor. Çelik üretimindeki güçlü büyüme ilk olarak yaklaşık 150 yıl önce ortaya çıkan çok sayıda teknolojik icat ve gelişmenin sonucunda meydana geldi. Buharla çalışan motorun ortaya çıkması çelik endüstrisine güçlü ve esnek bir tahrik sistemi sunmuş oldu; bol miktardaki taş kömüründen üretilen kok kömürü metalürjik prosesler için ideal bir yakıt ve redüksiyon maddesi oldu ve demir yolları ile buharlı gemilerdeki gelişmeler çelik için yeni ve büyük pazarlar oluşturdu.
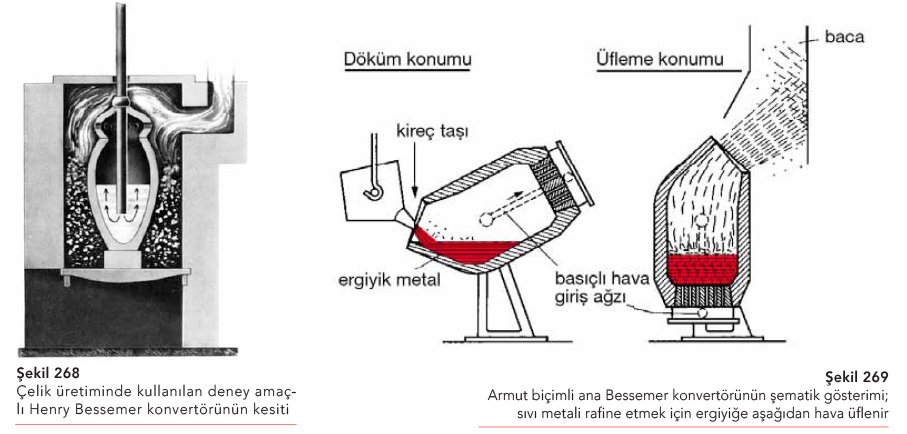
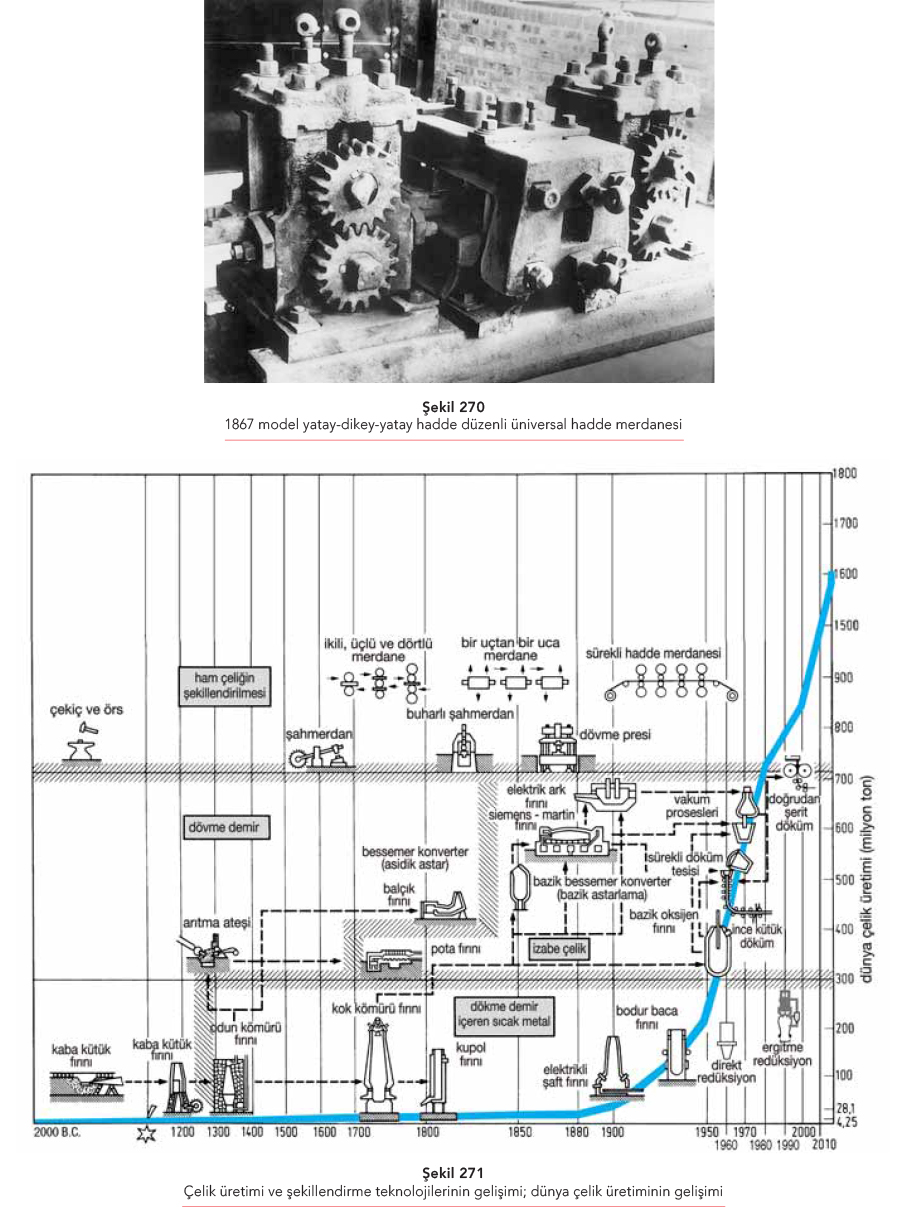