Onur MERİÇ (onur_meric@hotmail.com)
ÖZET
Mobil cihazların market yönelimleri gereği her geçen gün daha ince, daha hafif, daha hızlı, görüntü kalitesi daha iyi olması istenmektedir. Daha iyi görüntü kalitesi ve daha hızlı olması direk olarak ısı üretimini arttırırken, daha ince ve hafif olması da ürünün sağlamlığını ciddi riske sokmaktadır. Bu iki konunun değerlendirilmesinde tasarım göz ardı edilemez bir değişken olmak ile birlikte göreceli olarak malzeme seçimi de büyük önem taşımaktadır.
Bu çalışma, akıllı cep telefonu üretiminde içyapı malzemesi olarak en çok kullanılan alüminyum(ADC12) ve magnezyum(AZ91D) alaşımlarının termal analizlerini yaparak, malzemeler arasında optimizasyon yapmayı hedeflemektedir.
Anahtar kelimeler: Malzeme optimizasyonu, mobil ürün tasarımı, termal analiz, ADC12, AZ91D.
ABSTRACK
As necessitated by market trends, the demand for thinner, much lighter, much faster mobile devices with better visual quality is increasing every day. While better visual quality and improved fastness inrease heat production directly, thinner and lighter qualities put product robutsness in risk. Although design is a variable which can not be underestimated in consideration of these two subjects, material selection is also of great importance.
The purpose of this study is material optimization by thermal analysis of aluminum (ADC12) and magnesium (AZ91D) alloys which are most commonly used as internal structure part in smartphone manufacturing.
Keywords: Material optimization, mobile device design, thermal analysis, ADC12, AZ91D.
1. Giriş
Bu çalışma akıllı telefon tasarımı yapılırken seçilecek içyapı taşıyıcı parçasının ürün gerekliliklere göz önünde bulundurularak termal açıdan incelenmesi ve optimizasyonu amacı için yapılmıştır.
Akıllı telefon ürün tasarımı donanım, yazılım ve mekanik konuları içeren ortak bir çalışmasıdır ve ürün performansı bu ortak çalışmasının sonucu olarak
ortaya çıkar. Bu çalışmada tasarımı tamamlanmış bir ürün üzerinde, diğer parametreler sabit tutularak, içyapı taşıyıcı metal parçası için kullanılabilecek farklı malzemelerin ürüne etkisi incelenmiştir. Termal analizler için FloEFD, analiz programından yararlanılmıştır.
Termal analizlerde ürün için belirlenen ısı kaynak malzeme özellikleri atanmıştır. Bu parçaların farklı katmanları x, y, z doğrultularında farklı ısıl iletim katsayılarına sahiptir.
Sistemde panele ait 12 adet led ve bunun yanında 10 adet ısı kaynağı olarak tanımlanan entegre devresi(IC) mevcuttur. Anakart üzerindeki entegreleri soğutmak için entegreler üzerinde oluşan ısıyı içyapı taşıyıcı metaline aktarmak gerekmektedir. Bunun için termal arayüz malzemesi kullanılmıştır. Termal arayüz malzemesinin kullanım şekli Şekil 3.1’de gösterilmiştir.
Ürüne, pratikte ısıl çift kullanılarak yapılan kullanıcı ve güvenlik testlerinde ısının gözlemlendiği nokta ön cam bölgesindeki en fazla ısınan bölgedir, yapılan analizlerde de referans nokta olarak aynı bölge alınmıştır. Son kullanıcı testleri için belirtilen bölgelerde en yüksek güvenli sıcaklık 50 C° olarak belirlenmiştir. Ürünün cam ön yüzeyinin ve kullanın temas halinde olduğu yan alüminyum yüzeylerin, yapılan test ve analizlerde bu sıcaklığı aşmaması beklenir. Termal analiz için yapılan diğer kabuller aşağıdaki gibidir;
Şekil 3.1’de görülebileceği gibi malzemeler her iki yüzeye de tam olarak temas etmektedir.
• Isı kaynaklarının model üzerindeki pozisyonları Şekil 5.2 ve 5.3’te gösterilmiştir. Bu ısı kaynaklarına
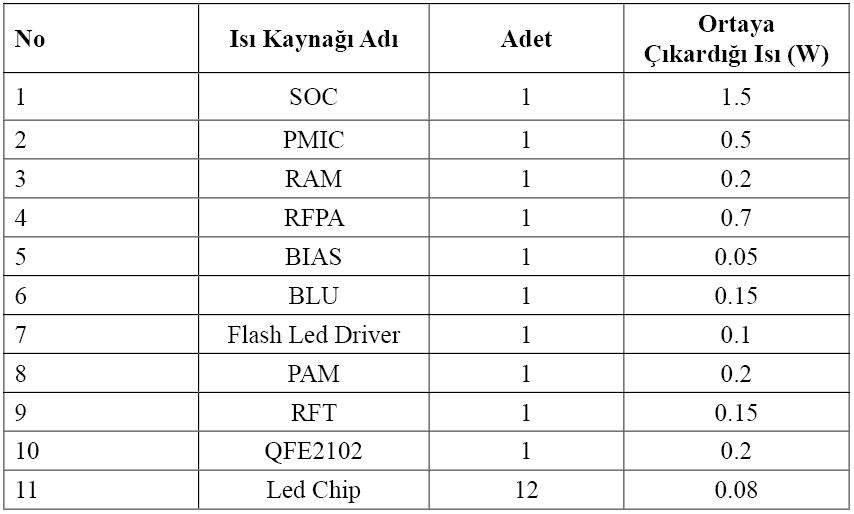
Şekil 3.1- Termal arayüz malzemelerimi gösterimi (kırmızı renkli) Çizelge 3.1- Isı Kaynakları ve Isı Kaynaklarına Ait Güç Değerleri
Ürüne, pratikte ısıl çift kullanılarak yapılan kullanıcı ve güvenlik testlerinde ısının gözlemlendiği nokta ön cam bölgesindeki en fazla ısınan bölgedir, yapılan analizlerde de referans nokta olarak aynı bölge alınmıştır. Son kullanıcı testleri için belirtilen bölgelerde en yüksek güvenli sıcaklık 50 C° olarak belirlenmiştir. Ürünün cam ön yüzeyinin ve kullanın temas halinde olduğu yan alüminyum yüzeylerin, yapılan test ve analizlerde bu sıcaklığı aşmaması beklenir. Termal analiz için yapılan diğer kabuller aşağıdaki gibidir;
• Ortam sıcaklığı: 25 C°
• Ürün yatay şekilde konumlandırılmıştır, yer çekimi –Z doğrultusundadır.
• PCB malzemesi: FR4
• Analiz senaryosuna göre tüm entegreler maksimum ısı verecek şekilde aynı anda çalışmaktadır.
• Entegreler ile içyapı taşıyıcı metali arasındaki ısı alışverişini sağlamak için ısı iletkenlik katsayısı 1.8 w/mK olan termal arayüz malzemeleri (TIM) kullanılmıştır.
• Isı kaynaklarının model üzerindeki pozisyonları Şekil 5.2 ve 5.3’te gösterilmiştir. Bu ısı kaynaklarına ait güç değerleri de Çizelge 5.1’de tanımlanmıştır.
• Genel mesh yapısı kullanılmış olup kullanılan hücre Sayısı 1.017.058’dir.
Şekil 3.3-Panel arka ışık ünitesindeki ısı kaynağı ledlerin gösterimi Şekil 3.2- Anakart üzerindeki ısı kaynaklarının gösterimi
2.2. Alüminyum Alaşımı (ADC12) Kullanılarak Yapılan Termal Analiz Sonuçları
Analiz, öncelikle içyapı taşıyıcı metali alüminyum alaşımı tanımlanarak yapılmıştır. Daha önce de belirtildiği üzere değerler son kullanıcının da temas edeceği cam yüzeyin ve alüminyum çerçevenin en yüksek ısı değerleri olarak alınmıştır. Şekil 3.4 ‘te de görüldüğü üzere anakart üzerindeki en yüksek ısı 97.06 0C’dir. Anakartta oluşan ısı, termal arayüz malzemesi yardımı ile entegreler üzerinden içyapı taşıyıcı metaline taşınır. İçyapı metalinin ısıl iletkenliği yüksek bir malzemeden yapılmasının istenmesinin sebebi; üzerinde taşınan bu ısının x ve y eksenlerinde dağıtarak, kullanıcının hissedeceği dış bölgeye daha az ısıyı taşımak ve taşınan ısının olabildiğince yayılarak sıcak noktalar oluşturmasını önlemektir.
Şekil 3.5’te içyapı taşıyıcı metalinden panele oradan da ön cama ulaşan ısının yoğunlaştığı bölgeler kırmızı renk ile gösterilmektedir. Bu bölgeler, ürün kullanımında son kullanıcının yüzüne temas etme olasılığı olduğu, özellikle dikkat edilen bölgelerdir. Yapılan analiz sonucunda ön camda görülen en yüksek ısı değerinin 48.83 0C olduğu gözükmektedir. Anakart üzerinde ısı oluşturan kaynaklar göze alındığında, ürünün alt kısmında yer alan panel ledlerinin genel sıcaklığı çok daha az etkilediği gözükmektedir.
Şekil 3.6’da diğer bir kritik bölge olan yan alüminyum çerçevenin yüzeyinden alınan analiz sonuçları verilmiştir. Yan alüminyum çerçeve yüzeyindeki en yüksek sıcaklık 42.12 0C’dir.
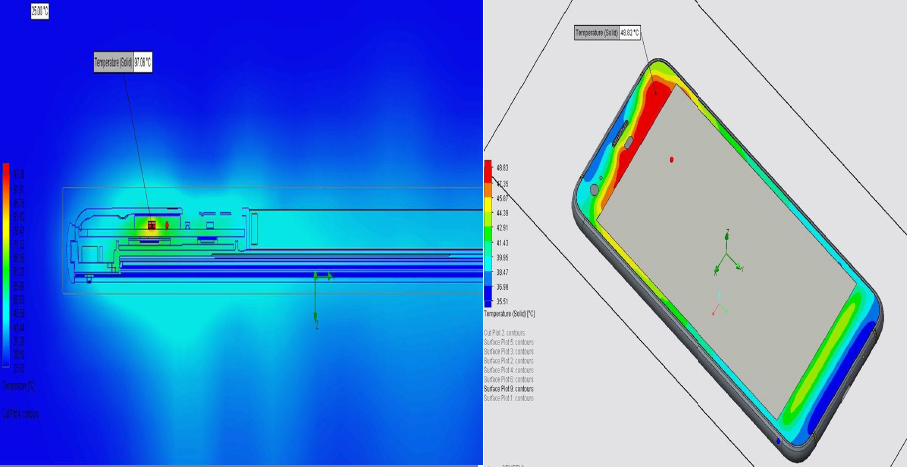
Şekil 3.4- Kesit ısı haritası anakart üzerindeki en yüksek sıcaklık 97.06 0C (ADC12) Şekil 3.5- Ön cam ısı dağılım haritası, kritik bölgedeki en yüksek sıcaklık 48.83 0C’dir. (ADC12)
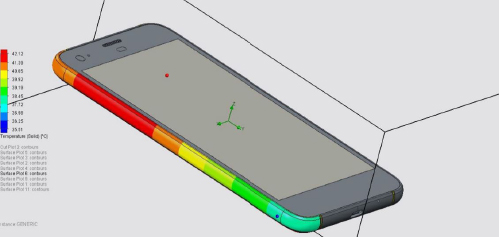
Şekil 3.6- Yan alüminyum çerçevedeki ısı dağılım haritası, kritik bölgedeki en yüksek sıcaklık 42.12 0C’dir. (ADC12)
Analiz sonuçları sonrasında ürün üzerinden alınan ölçümlerin ürün kriterlerine uygun ve güvenli sıcaklığın altında olduğu görülmektedir.
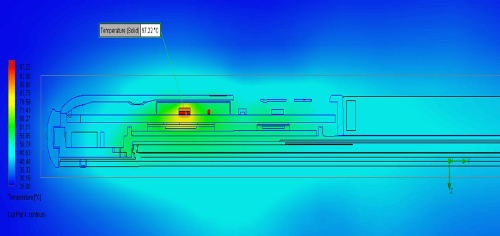
Şekil 3.7- Kesit ısı haritası anakart üzerindeki en yüksek sıcaklık 97.22 0C (AZ91D)
1.1. Magnezyum Alaşımı (AZ91D) Kullanılarak Yapılan Termal Analiz Sonuçları
İç yapı taşıyıcı malzemesi alüminyum alaşımı olarak tanımlanarak yapılan analiz sonrasında diğer tüm malzeme özellikleri ve şartlar aynı tutularak, sadece ilgili malzeme magnezyum olarak tanımlanmış ve analiz tekrarlanmıştır. Şekil 3.7’de belirtildiği üzere yapılan analiz sonrasında anakart üzerindeki en yüksek ısının 97.22 0C olduğu görülmüştür.
Şekil 3.8’da magnezyum alaşımı kullanılan analizde, ön cam yüzeyinde görülen en yüksek ısın 49.91 0C’dir.
Şekil 3.9’da yan alüminyum çerçeve üzerindeki en yüksek sıcaklığın 41.99 0C olduğu görülmektedir.
2. GENEL SONUÇLAR VE TARTIŞMA
Bu çalışmada, akıllı telefon tasarımı için mekanik ve termal özellikler Ansys ve FloEFD analiz programlarında incelenerek içyapı taşıyıcı parça için malzeme optimasyonu ve karakterizasyonu yapılmıştır. Bu araştıma için ADC12 alüminyum alaşımı ve AZ91D magnezyum alaşımı ele alınmıştır.
Çizelge 4.1’de görüldüğü üzere alüminyum alaşımının ısıl ve mukavemet değerleri magnezyum alaşımına göre daha iyi sonuç vermektedir.
Alüminyumun alaşımını ısıl değerleri magnezyum alaşımına göre daha iyi olsa da ürün için birbirine yakın değerlerdir. Sadece ısıl performans göz önüne alındığında market gereksinimleri gereği daha hafif bir ürün ortaya çıkarmak istendiğinde, ek pasif soğutma malzemeleri kullanılarak magnezyum alaşımı kullanımı da değerlendirilebilir.
Kaynaklar Dizini
NADCA 2015, NADCA Product Specification Standards for Die Casting, Arlington Heights, Illinois
Not: İlgili komponentlerin özellikleri sağlayıcı firmaların dökümanlarından referans alınmıştır. Anlaşma gereği paylaşılamamaktadır.
Çizelge 4.1- Isıl ve mekanik test sonuçlarının toplu ve karşılaştımalı gösterimi
Şekil 3.8- Ön cam ısı dağılım haritası, kritik bölgedeki Şekil 3.9 - Yan alüminyum çerçevedeki ısı dağılım haritası
en yüksek sıcaklık 49.91 0C’dir. AZ91D) kritik bölgedeki en yüksek sıcaklık 41.99 0C’dir. (AZ91D)